Water is widely considered as the second most destructive contamination to a lube system, after particulate contamination. This article will focus on how water exists in oil, the effects of water on oil and lube systems and measurement of water amount in oil, as well as setting alarm targets for water levels in oil.
Where does water come from?
Water in lubrication systems can originate from the environment, such as rain or moisture in the air. Leakage, damaged gasket on reservoir covers, underperforming air breathers, or a damaged wiper on a hydraulic cylinder are also possible sources. Condensation of air in oil reservoirs due to temperature difference between day and night will turn any moisture in the air into water droplets, mixing with the oil. A damaged water-based cooling system in a steam application is another potential water source.
How does water exist in oil?
Water in oil can exist in three stages: dissolved, emulsified and free. Below saturation level, the molecules of water are dispersed alongside oil molecules, resulting in water in the oil that is not visible. This is known as dissolved water, the least dangerous water state to a lube system.
When the amount of dissolved water exceeds the saturation point, the oil is no longer able to absorb more water molecules, resulting in emulsified water. This is characterised by a hazy or cloudy appearance of the oil.
Further increments of water content in oil will result in separate levels between oil and water forming. This state is known as free water. Due to its higher density, the water forms the lower layer, settling at the bottom of the sump, with the oil floating on top. However, emulsified water will also be present in an intermediate phase, continuing to circulate in the lube system.
Following figure shows the visible difference between dissolved, emulsified and free water within oil samples.
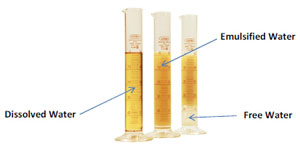
The saturation level of the oil is important, as it determines the amount of water that can be held before an emulsion will develop. Saturation level depends on base oil type, additive package, temperature and pressure. A highly refined mineral oil with minimum additive level has a saturation level of about 100 parts per million (ppm) at 70°F, whereas ester-based hydraulic fluids can have saturation levels of more than 3000 ppm at 70°F.
What type of damage can water do?
The effect of water in oil is twofold, destroying both the beneficial physical and chemical properties and characteristics of the oil. This can lead to machine component damage.
Effect on Oil
Physical
Higher viscosity
Reduced load carrying ability
Chemical
Hydrolysis - formation of acids, sludge and varnish
Reduced dielectric strength (transformer application)
Aeration - foam formation and air entrainment
Additive depletion
Effect on machinery
Corrosion on metal surfaces
Loss of lubrication film strength - Increased wear
Cavitation
Filter plugging
How is water in oil measured?
Water in oil can be measured in 3 ways; on-site by sampling, in the laboratory and online in real time.
1. On-site (offline application)
1.1 Crackle Test
The most expedient and economical way to determine water content in oil. Two drops of oil are placed on a hot surface (130℃) and any bubbling or crackling is observed. The size of bubbles may give an indication of the amount of water in the oil. However, due to its course and unitless results, a crackle test is suitable only as a screening test.
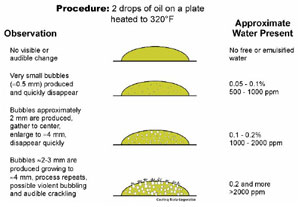
1.2 Calcium Hydride Test
One of the most widely used methods on-site; this method uses a pressurised call containing the oil sample and a chemical reagent (calcium hydride). Water in the oil reacts with the calcium hydride and forms hydrogen gas. The cell is shaken vigorously to accelerate the reaction. A change of pressure due to the hydrogen build up is detected by a pressure sensor and this is converted to a water content figure, either in % or part per million. The advantages of this method are a very fast turnaround (less than 4 minutes per test) and a low cost per sample.
2. Laboratory
2.1 Karl Fischer Method
One of the more accurate water tests, able to measure as low as 10 ppm of water in oil, but usually only available at a full service laboratory. A disadvantage of the Karl Fischer water test is that it is expensive and often time consuming when water concentrations are high.
2.2 Fourier Transform Infra-Red (FTIR)
FTIR is used as a rapid test for multiple parameters on an oil sample. Infra Red light is passed through a sample of oil and the absorption at different wavelengths in the optical spectra is measured and from this, the concentration of water can be determined. The technique also allows Nitration, Oxidation, Soot Concentration, Phosphate Anti-Wear and Anti-Oxidant depletion amongst other parameters.
3. On-line (Real Time Measurement)
3.1 Moisture Sensor
As the critically of water ingress increases, continuous monitoring of water in oil may be needed. On-line Moisture Sensors can be installed on machines where continuous, 24/7 monitoring is required.
3.2 On-line Infra-Red Measurement
This measures the water content in parts per million within the oil by utilising absorption of infrared light by the water in the oil. This method has the advantage of being able to measure the total water content (dissolved, emulsified and free water). It can also measure soot content within the oil at the same time data is logged within the device and alarms can be set for notification purposes. The data can also be transferred directly to a PC or downloaded via a USB drive.