EXPLANATION
The thermal stress experienced by aviation fuel in modern jet engines may lead to the formation of undesirable and possibly harmful insoluble materials, such as lacquers, on heat exchangers and control surfaces, that reduce efficiency and require extra maintenance. Aircraft fuel systems operate mainly under turbulent flow conditions. Most large scale realistic test rigs operate in the turbulent flow regime but fuel volumes are very large and test times are very long. This test method tests fuel under turbulent flow (high Reynolds number) conditions, and it gives a quantitative result under standard operating conditions of 65 or 125 min. Continuous analysis of the results during the test allows performance of the fuel to be monitored in real time thus enabling the test time to be reduced manually or automatically, if required. The results of this test method are not expected to correlate with existing test methods for all fuels, since the test methods and the operating conditions are different.
This test method covers a laboratory thermal process using a specified apparatus for measuring the tendencies of aviation turbine fuels to deposit insoluble materials and decomposition products, such as lacquers, within a fuel system.
TEST SUMMARY
Fuel is pumped at pressure, through an electrically heated capillary tube at a constant rate. The heating of the capillary tube is controlled to maintain a constant fuel temperature of 290 +/- 3°C at the exit of the capillary tube. A flow rate greater than 20 mL/min and the specified capillary bore of less than 300 mm ensures that turbulent flow is maintained within the capillary. The formation of lacquers and fuel degradation products act as a thermal insulator between the cooler fuel and hotter capillary tube, resulting in an increase in temperature of the capillary tube which is measured at a number of positions by a contactless pyrometer. The HiReTS Total (T) number is displayed during and at the end of the test. The HiReTS Peak (P) number can be determined from analysis of the results.
CORRELATIONS
(1) Some test programs have shown a strong correlation between carbon burn off measurements from used capillary tubes and their respective HiReTS results.
(2) Correlation between JFTOT D 3241 and this test method is unlikely due to the difference between the two test methods, and with HiReTS operating in the turbulent flow regime using stainless tubes, and the JFTOT operating in the laminar flow regime using aluminum tubes. A HiReTS Reynolds number of greater than 5000 can be contrasted with a JFTOT Reynolds number of 11.
TEST PRECISION
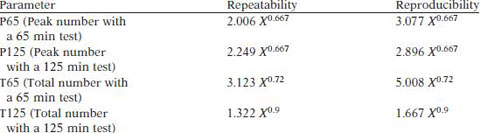
Where X is the average of results being compared. The precision applies only to HiReTS Peak numbers up to 200 and Total numbers up to 1900; higher values can be measured but the precision estimates may not apply. This test method has no bias because the result of the test is defined only in terms of this test method.