By John S. Evans, B.Sc.
LUBRICATION
The friction that exists between two bodies in relative motion involves an appreciable energy loss which needs to be minimised. This is achieved by feeding lubricants between these sliding surfaces which replace solid friction with fluid friction which can be far smaller.
A lubricant must possess two basic properties: some degree of fluidity to spread over the surfaces and adhesive power to allow the fluid to remain in place during motion. Oils are particularly well suited to this job.
When an oil is fed in between two moving surfaces it causes them to separate and in doing so eliminates the solid friction that exists between them. Unfortunately viscous drag (fluid friction) exists in the oil so that friction can never be totally eliminated but it can be greatly reduced. The oil can cause the surfaces to separate in a number of ways and, when this is not completely possible, friction is still kept to a manageable level.
The lubrication regimes that will be considered here are: boundary lubrication, mixed film lubrication and hydrodynamic lubrication which includes elastohydrodynamic lubrication (EHD).
Boundary lubrication
Three parameters need to be considered when looking at the various lubrication regimes. They are: the load placed on the surfaces, the speed at which they are moving relative to each other, and the viscosity of the lubricant.
Viscosity is a very important property of a lubricant and will be defined at this point as a fluid's resistance to flow at a particular temperature. Fluids that have high viscosities do not flow easily (such as molasses) - high viscosity oils are sometimes referred to as 'thick' oils. Fluids with low viscosities flow easily (such as water) - low viscosity oils are sometimes referred to as 'thin' oils.
It is important to remember that when an oil is heated up, its viscosity will decrease. In other words, it will 'thin out'. Likewise the viscosity will increase as the temperature decreases and the oil will 'thicken up'. Because of this an oil's viscosity must always be accompanied by the temperature at which the measurement was made for it to mean anything.
In a situation for ideal lubrication the viscosity and the speed should be high and the load low. If this were always the case then lubricated surfaces would always be separated and only fluid friction would come into play. Unfortunately we do not live in an ideal world and this is not always possible.
In the case of a plain bearing and a journal there will be a small amount of lubricant between the mating surfaces. However, because of the load and zero speed on start up, the lubricant film will not completely separate the bearing from the journal. In this situation the asperities will break through the lubricant film and make contact; this is known as boundary lubrication. All is not lost, however, and the situation is far better than if no oil were present at all. Typically, the coefficient of friction of unlubricated metal surfaces ranges between 1.5 and 0.5. With boundary lubrication it is between 0.1 and 0.02.
Boundary lubrication can be sub-divided into: oily lubrication, anti-wear lubrication and EP (extreme pressure) lubrication.
1. Oily lubrication takes place through two distinct mechanisms:
(1) Physical adsorption, whereby oil molecules and compounds blended into the oil are attracted electrostatically to metal surfaces and form bimolecular layers due to the polar nature of these compounds.
(2) A chemical reaction also takes place causing certain compounds in the oil to attach themselves chemically to the metal surfaces. This allows very thin films, usually only one or two molecules thick, to form and help reduce friction whilst not totally separating the metal surfaces (see Diagram 3).
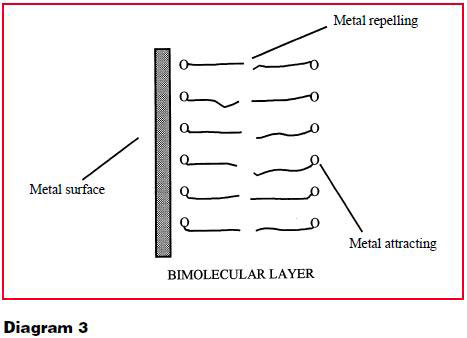
2. Antiwear lubrication occurs because of the presence of chemical compounds in the oil that are specifically designed to react with metal surfaces and form a protective layer. The melting point of these compounds is fairly low and is below the temperature at which EP compounds are effective. Antiwear additives are sometimes referred to as mild EP additives.
3. EP lubrication is required where high pressures and hence high temperatures are encountered. This is achieved by the addition of compounds that contain phosphorus and sulphur that react with the metal surfaces to form compounds such as iron sulphide which has a high melting point and low shear strength. In other words, they make the metal surfaces slippery.
Mixed film lubrication
The coefficient of friction in a plain bearing is related to the load on the bearing, the speed at which it is turning and the viscosity of the oil that is lubricating the system.
Assuming the viscosity remains constant throughout (as will the load) then the coefficient of friction will vary with the change in speed. On start-up the speed is low (zero) so that the coefficient of friction will be high but will decrease as the speed increases. The graph below illustrates the relationship where initially the solid friction is very high but is gradually replaced with fluid friction as the journal begins to turn. Mixed film lubrication occurs when boundary lubrication is reduced but the mating surfaces are not quite separated and are supported by a full film of lubricant (see Diagram 4).
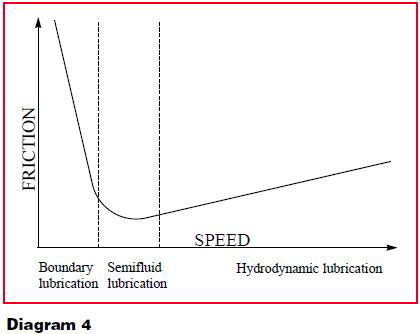
Hydrodynamic lubrication
In theory the journal should be located coaxially with the bearing. However, in practice, this does not happen unless the load is extremely small or the shaft is mounted vertically. In practical cases there is an appreciable load on the oil film and the journal cannot rotate coaxially to the bearing.
As speed increases a wedge is formed between the converging surfaces through which the oil is forced as it is entrained by the rotating shaft. At this point the fluid has a greater velocity, and hydrodynamic pressure is created which counterbalances the load and keeps the mating surfaces apart.
Under this type of lubrication regime the coefficient of friction is reduced to the order of 0.005. It will be noted from the graph that the minimum friction is achieved just before the onset of hydrodynamic lubrication. It is at this point that solid or static friction is replaced by fluid or kinematic friction. Unlike solid friction, fluid friction is dependant on speed and gradually increases as the speed increases.
Elastohydrodynamic lubrication (EHD)
The surfaces in relative motion that require lubrication that have been considered so far have had the same geometry, that is they fit together like two spoons. In the case of a ball or roller bearing, the contact area between the mating surfaces is vanishingly small. With a ball bearing in a race, the area of contact is a tangential point and, with a roller bearing, a tangential line. Remember that pressure is defined as force over area and in this situation the area is very small. With normal loads in roller elements, pressures of 1.5 Gpa (1,5 million kilopascals) can be reached. Under these conditions both the roller elements and the oil behave in a non-Newtonian fashion (see Newtonian fluids section on back page).
These high pressures are known as Hertzian pressures and the point or line of contact of the roller is known as the Hertzian region. These high pressures cause both the roller and the race to elastically deform to a small degree which spreads the pressure over a small but finite area. Oil is drawn into the Hertzian region by hydrodynamic forces and when subjected to these Hertzian pressures the viscosity increases (reversibly) dramatically and has the consistency of window putty. It is this increase in viscosity that enables the oil to lubricate under these extreme conditions and this lubrication regime is known as elastohydrodynamic lubrication.