5. Apparatus
5.1 Centrifuge - A centrifuge shall be capable of spinning two or more centrifuge tubes at a speed that can be controlled to give a minimum relative centrifugal force of 500 at the tip of the tubes. The rotation speed necessary to produce a relative centrifugal force of 500 for various diameters of swing can be determined from Table 1 or from one of the following equations:
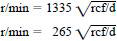
where:
rpm = rotation speed, in revolutions per minute.
rcf = relative centrifugal force,
d = diameter of swing, in mm (Eq 1) or in. (Eq 2), measured between the tips of opposite tubes when the tubes are in their rotating position.
The revolving head, trunnion rings, and trunnion cups, including the cushions, shall be constructed to withstand the maximum centrifugal force capable of being delivered by the power source. The trunnion cups and cushions shall firmly support the tubes when the centrifuge is in motion. The centrifuge shall be enclosed by a metal shield or case strong enough to contain flying debris in the event a tube breaks or the centrifuge malfunctions.
5.1.1 The centrifuge shall be heated and shall be capable of maintaining the sample at a temperature of 60°C +/- 3°C (140°F +/- 5°F). The minimum allowable temperature in the field shall be 52°C (125°F).
5.2 Centrifuge Tubes:
5.2.1 Centrifuge tubes shall be cone shaped and 203 mm (8 in.) or 167 mm (6 in.) in length. Tubes shall conform to the dimensions given in Fig. 1 (203 mm) or Fig. 2 (167 mm) and shall be made of thoroughly annealed glass. A200-part tube shall conform to the dimensions shown in Fig. 2, with the marking for each division multiplied by 2 (for example, 25 mL = 50 parts). The mouth of each tube shall be constricted for closure with a stopper. Graduations for the 203-mm (8-in.) and 167-mm (6-in.) tubes shall be in accordance with the requirements of Table 2 and Table 3, respectively. The scale errors for a centrifuge tube shall not exceed the tolerances specified in Table 2 and Table 3. The graduation requirements and scale-error tolerances shown in Table 2 and Table 3 apply to calibrations made by reading the bottom of the shaded meniscus of air-free water at a temperature of 20°C (68°F). The graduations on each tube shall be clearly numbered as shown in Fig. 1 and Fig. 2.
5.2.2 The tube graduation marks' accuracy shall be volumetrically verified or gravimetrically certified before field use of the tube, in accordance with Practice E 542 using National Institute of Standards and Technology-traceable equipment. The verification or certification shall include a calibration check at each mark up through the 0.5-mL (1-part) mark; at the 1-, 1.5-, and 2-mL (2-, 3-, and 4-part) marks: and at the 50- and 100-mL (100- and 200-part) marks. The tube shall not be used if the scale error at any mark exceeds the applicable tolerance from Table 2 or 3.
5.3 Preheater - The preheater shall be either a metal block or a liquid bath of sufficient depth to permit immersion of the centrifuge tube in the vertical position to the 100-mL litre (200-part) mark and capable of heating the sample to 60°C +/- 3°C (140°F +/- 5°F).
5.4 Thermometer shall have graduations at intervals of 1°C (2°F) or less and shall be accurate to +/-1°C (+/-2°F). A thermometer such as ASTM 1C or 1F is suitable as shown in Specification E 1.
6. Reagents
6.1 The reagents listed in this section are satisfactory for use in field testing.
6.2 Demulsifier - When necessary, a demulsifier should be used to promote the separation of water from the sample, to prevent water from the sample, clinging to the walls of the centrifuge tube, and to enhance the distinctiveness of the water-oil interface. In some cases a demulsifier is required to attain agreement with the base method (see Note 1). When a demulsifier is used, it should be mixed according to the manufacturer's recommendations and should never add to the volume of sediment and water determined. The demulsifier should always be used in the form of a demulsifier-solvent stock solution or be premixed with the solvent to be used in the test.
6.3 Kerosine (Specification D 3699)
6.3.1 The typical characteristics of kerosine are a distillation range of 205-300°C (401-572°F), a maximum freezing point of -30°C (-22°F), and a minimum flash point of 38°C (100°F).
6.3.2 Stoddard solvent and kerosine do not have to be saturated with water, since the solubility of water in these solvents is not significant at 60°C (140°F).
NOTE 3 - Warning: Kerosine is combustible (See A1.1).
6.4 Stoddard Solvent (Specification D235):
6.4.1 The typical characteristics of Stoddard solvent are a distillation range of 149-208°C (300-407°F), a minimum flash point of 38°C (100°F), and aromatics plus olefins content of less than 20 % by volume.
NOTE 4 - Warning: Stoddard solvent is combustible (See A1.2).
6.4.2 See 6.3.2.
6.5 Toluene (Specification D 362):
6.5.1 The typical characteristics of toluene are a molecular weight of 92, an American Public Health Association (APHA) color of 10 (in accordance with Test Method D1209), a boiling range (initial to dry point) of 2.0°C (3.6°F) [recorded boiling point of 110.6°C (231.1°F)], and 0.001 % residue after evaporation. Toluene passes the American Chemical Society (ACS) test for substances darkened by H2SO4.
NOTE 5 - Warning: Toluene is flammable (See A1.3).
6.5.2 Toluene and xylene shall be saturated with water at 60°C +/- 3°C (140°F +/- 5°F) and maintained at this temperature until used. A procedure for the saturation of solvents is given in the appendix. The water-saturated solvent shall be free from suspended water at the time of use. Toluene and xylene are recommended for sediment-and-water determinations involving asphaltenic crude oils.
6.6 Xylene (Specification D846):
6.6.1 The typical characteristics of xylene are a molecular weight of 106, an APHA color of not more than 10 (in accordance with Test Method D1209), a boiling range of 137 to 144°C (279 to 291°F), and 0.002 % residue after evaporation. Xylene passes the ACS test for substances darkened by sulfuric acid.
NOTE 6 - Warning: Xylene is flammable (See A1.4).
6.6.2 See 6.5.2.
7. Sampling
7.1 Sampling is defined as all steps required to obtain a representative quantity of the contents of any pipeline, tank, or other system and to place it in an appropriate centrifuge tube.
7.2 The sample shall be thoroughly representative of the crude oil in question, and the portion of the sample used for the sediment and water determination shall be thoroughly representative of the sample itself. If an automatic custody transfer (LACT) unit is involved, vigorous agitation of the sample container is required before the sample is transferred to the centrifuge tube or tubes. Only representative samples obtained as specified in Practices D4057 or D4177 shall be used for this test method.