1. Scope
1.1 This test method covers an engine test procedure for evaluating automotive engine oils for certain high-temperature performance characteristics, including oil thickening, varnish deposition, oil consumption, as well as engine wear. Such oils include both single viscosity grade and multiviscosity grade oils that are used in both spark-ignition, gasoline-fueled engines, as well as in diesel engines.
1.1.1 Additionally, with nonmandatory supplemental requirements, a IIIGA Test (Mini Rotary Viscometer and Cold Cranking Simulator measurements), a IIIGVS Test (EOT viscosity increase measurement), or a IIIGB Test (phosphorous retention measurement) can be conducted. These supplemental test procedures are contained in Appendixes Appendix X1, Appendix X2, and Appendix X3, respectively.
NOTE 1 - Companion test methods used to evaluate engine oil performance for specification requirements are discussed in SAE J304.
1.2 The values stated in SI units are to be regarded as standard. No other units of measurement are included in this standard.
1.2.1 Exception - Where there is no direct SI equivalent such as screw threads, national pipe threads/diameters, and tubing size.
1.3 This standard does not purport to address all of the safety concerns, if any, associated with its use. It is the responsibility of the user of this standard to establish appropriate safety and health practices and determine the applicability of regulatory limitations prior to use. Specific warning statements are provided in 6.14.1.1 and 7.1.
1.4 This test method is arranged as follows:
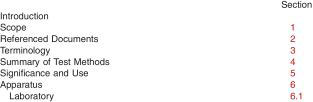
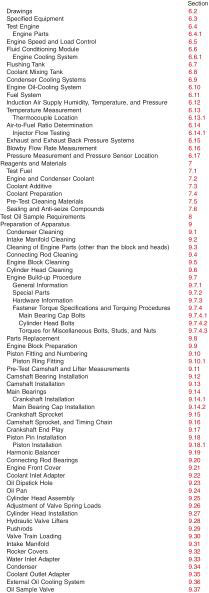
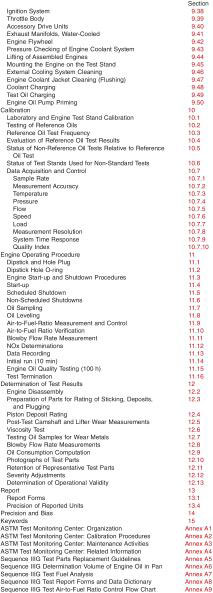
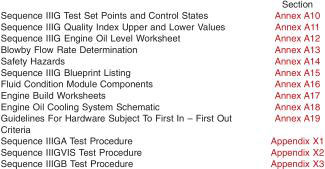
2. Referenced Documents
2.1 ASTM Standards:
D86 Test Method for Distillation of Petroleum Products and Liquid Fuels at Atmospheric Pressure
D130 Test Method for Corrosiveness to Copper from Petroleum Products by Copper Strip Test
D235 Specification for Mineral Spirits (Petroleum Spirits) (Hydrocarbon Dry Cleaning Solvent)
D240 Test Method for Heat of Combustion of Liquid Hydrocarbon Fuels by Bomb Calorimeter
D323 Test Method for Vapor Pressure of Petroleum Products (Reid Method)
D381 Test Method for Gum Content in Fuels by Jet Evaporation
D445 Test Method for Kinematic Viscosity of Transparent and Opaque Liquids (and Calculation of Dynamic Viscosity)
D525 Test Method for Oxidation Stability of Gasoline (Induction Period Method)
D1319 Test Method for Hydrocarbon Types in Liquid Petroleum Products by Fluorescent Indicator Adsorption
D2699 Test Method for Research Octane Number of Spark-Ignition Engine Fuel
D2700 Test Method for Motor Octane Number of Spark-Ignition Engine Fuel
D3231 Test Method for Phosphorus in Gasoline
D3237 Test Method for Lead in Gasoline by Atomic Absorption Spectroscopy
D3244 Practice for Utilization of Test Data to Determine Conformance with Specifications
D3338 Test Method for Estimation of Net Heat of Combustion of Aviation Fuels
D3343 Test Method for Estimation of Hydrogen Content of Aviation Fuels
D4052 Test Method for Density, Relative Density, and API Gravity of Liquids by Digital Density Meter
D4175 Terminology Relating to Petroleum Products, Liquid Fuels, and Lubricants
D4485 Specification for Performance of Active API Service Category Engine Oils
D4684 Test Method for Determination of Yield Stress and Apparent Viscosity of Engine Oils at Low Temperature
D4815 Test Method for Determination of MTBE, ETBE, TAME, DIPE, tertiary-Amyl Alcohol and C1 to C4 Alcohols in Gasoline by Gas Chromatography
D5185 Test Method for Multielement Determination of Used and Unused Lubricating Oils and Base Oils by Inductively Coupled Plasma Atomic Emission Spectrometry (ICP-AES)
D5191 Test Method for Vapor Pressure of Petroleum Products (Mini Method)
D5293 Test Method for Apparent Viscosity of Engine Oils and Base Stocks Between -10 °C and -35 °C Using Cold-Cranking Simulator
D5452 Test Method for Particulate Contamination in Aviation Fuels by Laboratory Filtration
D5453 Test Method for Determination of Total Sulfur in Light Hydrocarbons, Spark Ignition Engine Fuel, Diesel Engine Fuel, and Engine Oil by Ultraviolet Fluorescence
D5862 Test Method for Evaluation of Engine Oils in Two-Stroke Cycle Turbo-Supercharged 6V92TA Diesel Engine (Withdrawn 2009)
D6593 Test Method for Evaluation of Automotive Engine Oils for Inhibition of Deposit Formation in a Spark-Ignition Internal Combustion Engine Fueled with Gasoline and Operated Under Low-Temperature, Light-Duty Conditions
D6750 Test Methods for Evaluation of Engine Oils in a High-Speed, Single-Cylinder Diesel Engine - 1K Procedure (0.4 % Fuel Sulfur) and 1N Procedure (0.04 % Fuel Sulfur)
D6984 Test Method for Evaluation of Automotive Engine Oils in the Sequence IIIF, Spark-Ignition Engine
D7422 Test Method for Evaluation of Diesel Engine Oils in T-12 Exhaust Gas Recirculation Diesel Engine
E29 Practice for Using Significant Digits in Test Data to Determine Conformance with Specifications
E191 Specification forApparatus For Microdetermination of Carbon and Hydrogen in Organic and Organo-Metallic Compounds
E608/E608M Specification for Mineral-Insulated, Metal-Sheathed Base Metal Thermocouples
E1119 Specification for Industrial Grade Ethylene Glycol
IEEE/ASTM SI 10 Standard for Use of the International System of Units (SI): The Modern Metric System
2.2 Military Specification:
MIL-PRF-2104, Lubricating Oil, Internal Combustion Engine, Tactical Service
2.3 SAE Standards:
J183, Engine Oil Performance and Engine Service Classification (Other Than "Energy-Conserving")
J300, Engine Oil Viscosity Classification *HS-23/00
J304, Engine Oil Tests
2.4 Other ASTM Documents:
Guidelines for Calibration
The Lubricant Test Monitoring System, Sequence IIIG Test Control Chart Technique for Developing and Applying Severity Adjustments (SA)
ASTM Deposit Rating Manual 20 (Formerly CRC Manual 20)
3. Terminology
3.1 Definitions:
3.1.1 blowby, n - in internal combustion engines, that portion of the combustion products and unburned air/fuel mixture that leaks past piston rings into the engine crankcase during operation.
3.1.2 BTDC (before top dead center), n - used with the degree symbol to indicate the angular position of the crankshaft relative to its position at the point of uppermost travel of the piston in the cylinder.
3.1.3 calibrate, v - to determine the indication or output of a device (e.g., thermometer, manometer, engine) with respect to that of a standard.
3.1.4 clogging, n - the restriction of a flow path due to the accumulation of material along the flow path boundaries.
3.1.5 cold-stuck piston ring, n - in internal combustion engines, a piston ring that is stuck when the piston and ring are at room temperature, but inspection shows that it was free during engine operation.
3.1.5.1 Discussion - A cold-stuck piston ring cannot be moved with moderate finger pressure. It is characterized by a polished face over its entire circumference, indicating essentially no blowby passed over the outside of the ring during operation.
3.1.6 correction factor, n - a mathematical adjustment to a test result to compensate for industry wide shifts in severity.
3.1.7 corrosion, n - the chemical or electrochemical reaction between a material, usually a metal surface, and its environment that can produce a deterioration of the material and its properties.
3.1.8 debris, n - in internal combustion engines, solid contaminant materials unintentionally introduced into the engine or resulting from wear.
3.1.9 engine oil, n - a liquid that reduces friction or wear, or both, between the moving parts within an engine; removes heat, particularly from the underside of pistons; and serves as a combustion gas sealant for piston rings.
3.1.9.1 Discussion - It may contain additives to enhance certain properties. Inhibition of engine rusting, deposit formation, valve train wear, oil oxidation, and foaming are examples.
3.1.10 EWMA, n - abbreviation for exponentially-weighted moving average.
3.1.11 free piston ring, n - in internal combustion engines, a piston ring that will fall in its groove under the force of its own weight when the piston with the ring in a horizontal plane, is turned 90° (putting the ring in a vertical plane).
3.1.11.1 Discussion - In determination of this condition, the ring may be touched slightly to overcome static friction.
3.1.12 hot-stuck piston ring, n - in internal combustion engines, a piston ring that is stuck when the piston and ring are at room temperature, and inspection shows that it was stuck during engine operation.
3.1.12.1 Discussion - The portion of the ring that is stuck cannot be moved with moderate finger pressure. A hot-stuck ring is characterized by varnish or carbon across a portion of its face, indicating that portion of the ring was not contacting the cylinder wall during engine operation.
3.1.13 Lubricant Test Monitoring System (LTMS), n - an analytical system in which ASTM calibration test data are used to manage lubricant test precision and severity (bias).
3.1.14 LTMS date, n - the date the test was completed unless a different date is assigned by the TMC.
3.1.15 LTMS time, n - the time the test was completed unless a different time is assigned by the TMC.
3.1.16 lubricant, n - any material interposed between two surfaces that reduces the friction or wear, or both, between them.
3.1.17 lubricating oil, n - a liquid lubricant, usually comprising several ingredients, including a major portion of base oil and minor portions of various additives
3.1.18 Material Safety Data Sheet, (MSDS), n - a fact sheet summarizing information about material identification; hazardous ingredients; health, physical, and fire hazards; first aid; chemical reactivities and incompatibilities; spill, leak, and disposal procedures; and protective measures required for safe handling and storage.
3.1.19 non-compounded engine oil, n - a lubricating oil having a viscosity within the range of viscosities of oils normally used in engines, and that may contain anti-foam agents or pour depressants, or both, but not other additives.
3.1.20 non-reference oil, n - any oil, other than a reference oil; such as a research formulation, commercial oil, or candidate oil.
3.1.21 oxidation, n - of engine oil, the reaction of the oil with an electron acceptor, generally oxygen, that can produce deleterious acidic or resinous materials often manifested as sludge formation, varnish formation, viscosity increase, or corrosion, or a combination thereof.
3.1.22 quality index (QI), n - a mathematical formula that uses data from controlled parameters to calculate a value indicative of control performance.
3.1.23 reference oil, n - an oil of known performance characteristics, used as a basis for comparison.
3.1.23.1 Discussion - Reference oils are used to calibrate testing facilities, to compare the performance of other oils, or to evaluate other materials (such as seals) that interact with oils.
3.1.24 rust (coatings), n - of iron or its alloys, a corrosion product consisting of hydrated iron oxides, usually reddish in color, but can also be brown-to-black.
3.1.25 SA, n - abbreviation for severity adjustment.
3.1.26 scoring, n - in tribology, a severe form of wear characterized by the formation of extensive grooves and scratches in the direction of sliding.
3.1.27 scuffıng, n - in lubrication, damage caused by instantaneous localized welding between surfaces in relative motion that does not result in immobilization of the parts.
3.1.28 test oil, n - any oil subjected to evaluation in an established procedure.
3.1.28.1 Discussion - It can be any oil selected by the laboratory conducting the test. It could be an experimental product or a commercially available oil. Often, it is an oil that is a candidate for approval against engine oil specifications (such as manufacturers' or military specifications, etc.).
3.1.29 test procedure, n - one where test parameters, apparatus, apparatus preparation, and measurements are principal items specified.
3.1.30 used oil, n - any oil that has been in a piece of equipment (for example, an engine, gearbox, transformer, or turbine), whether operated or not.
3.1.31 varnish, n - in internal combustion engines, a hard, dry, generally lustrous, deposit that can be removed by solvents but not by wiping with a cloth.
3.1.32 wear, n - the loss of material from a surface, generally occurring between two surfaces in relative motion, and resulting from mechanical or chemical action or a combination of both.
3.2 Definitions of Terms Specific to This Standard:
3.2.1 build-up oil, n - EF-411, non-compounded, ISO VG 32 (SAE 10) oil used in lubricating some of the Sequence IIIG parts during engine assembly.
3.2.2 calibrated test stand, n - a test stand on which Sequence IIIG engine oil tests are conducted within the LTMS as administered by the TMC. (See 10.1.)
3.2.3 central parts distributor (CPD), n - the manufacturer and supplier of many of the parts and fixtures used in this test method.
3.2.3.1 Discussion - Because of the need for rigorous inspection and control of many of the parts used in this test method, and because of the need for careful manufacture of special parts and fixtures used, companies having the capabilities to provide the needed services have been selected as the official suppliers for the Sequence IIIG test method. These companies work closely with the original parts suppliers, with the Test Procedure Developer, and with the ASTM groups associated with the test method to help ensure that the equipment and materials used in the method function satisfactorily.
3.2.4 special test parts (STP), n - parts that do not meet all the definitions of critical parts, non-production parts, or SPO parts, but shall be obtained only from the specified distributor.
3.2.5 critical parts (CP), n - those components used in the test, which are known to affect test severity.
3.2.5.1 Discussion - Critical parts shall be obtained from the Central Parts Distributor or Special Parts Supplier, who will identify them with either a serial number or a batch/lot control number.
3.2.6 EOT time (end of test time), n - 20 min after the engine reaches 100 test h of operation, which allows 120 s for ramp-down/idle, a 15 min wait for oil to drain into the sump, and allows the operator 3.0 min to measure oil level.
3.2.7 non-production parts (NP), n - components used in the test, which are available only through the Central Parts Distributor, Special Parts Supplier, or the Test Procedure Developer.
3.2.8 participating laboratory, n - a laboratory equipped to conduct Sequence IIIG tests, which conducts reference oil tests in cooperation with the TMC, in order to have calibrated test stands available for non-reference oil testing.
3.2.9 pinched piston ring, n - an installed piston ring which will not move in its groove under moderate finger pressure, but which has a polished face over its entire circumference indicating that it was free during engine operation; The ring may be restricted over varying degrees of its circumference.
3.2.10 reference oil test, n - a standard Sequence IIIG engine oil test of a reference oil designated by the TMC.
3.2.11 service parts operations parts (SPO), n - these test components are obtained from Service Parts Operations a division of General Motors Corporation.
3.2.12 sluggish piston ring, n - an installed piston ring which it offers resistance to movement in its groove, but it can be pressed into or out of the groove under moderate finger pressure; when so moved, it does not spring back (one that is neither free nor stuck).
3.2.13 special parts supplier, (SPS), n - the manufacturer and supplier of many of the parts and fixtures used in this test method.
3.2.14 special test parts, n - parts that do not meet all the definitions of critical parts, non-production parts, or SPO parts, but shall be obtained from the Special Parts Supplier.
3.2.15 standard test, (valid test), n - an operationally valid, full-length Sequence IIIG test conducted on a calibrated test stand in accordance with the conditions listed in this standard.
3.2.16 stuck piston ring, n - one that is either partially or completely bound in its groove and cannot be readily moved with moderate finger pressure.
3.2.17 test procedure developer, n - the group or agency which developed the Sequence IIIG test procedure before its standardization by ASTM, and which continues to be involved with the test in respect to modifications in the test method, development of Information Letters, supply of test parts, and so forth.
3.2.17.1 Discussion - In the case of the Sequence IIIG test, the Test Procedure Developer is General Motors Research and Development Center.
3.2.18 test full mark, n - the oil level established after the 10-min initial run-in.
3.2.19 test stand, n - a suitable foundation (such as a bed-plate) to which is mounted a dynamometer, and which is equipped with a suitable data acquisition system, fluids process control system, supplies of electricity, compressed air, and so forth, to provide a means for mounting and operating an engine in order to conduct a Sequence IIIG engine oil test.
3.2.20 test start, n - introduction of test oil into the engine after the final assembly and mounting in the test stand.
3.2.21 test start time, n - the time that test oil was introduced into the engine on the test stand.