9. Sampling
9.1 The objective of sampling is to obtain a test specimen that is representative of the entire quantity. Thus, take laboratory samples in accordance with the instructions in Practice D4057. The specific sampling technique can affect the accuracy of this test method.
10. Preparation of Samples
10.1 Sulfated Ash Digestion:
10.1.1 Accurately weigh approximately 1 to 2 +/- 0.1 g of the grease sample in a Vycor or platinum container of suitable size. Char the sample on a hot plate until it is reduced to ~0.5 g. A heat lamp may be used to assist in this process.
10.1.2 After the charred residue is cooled, add 1 to 2 mL of concentrated sulfuric acid and carefully heat on the hot plate taking care to avoid spattering of the contents, and continue heating until the fumes are no longer evolved.
10.1.3 Place the charred sample in a muffle furnace at 525 +/- 25°C until the oxidation of the carbon is practically complete. This typically takes about 2 h.
10.1.4 If the ashing is not complete as indicated by presence of black color of the residue, repeat step 10.1.2 to complete the sulfation.
10.1.5 Add about 5 mL of concentrated nitric, hydrochloric or other appropriate mineral acid to the residue, and heat gently to dissolve the remaining solids.
10.1.6 Dilute the solution to volume with deionized water in a 25 or a 50 mL volumetric flask.
NOTE 1 - The dilutions may be carried out on a weight or volume basis.
10.2 Closed Vessel Microwave Oven Digestion:
10.2.1 Accurately weigh about 0.1 to 1 g of the grease sample in a polytetrafluoroethylene (PTFE) digestion vessel with pressure relief mechanism. Add about 4 mL of concentrated nitric, hydrochloric, or other appropriate mineral acid.
NOTE 2 - From a safety view point when digesting samples containing volatile or easily oxidized organic compounds, initially weigh no more than 0.10 g and observe the reaction before capping the vessel. If a vigorous reaction occurs, allow the reaction to cease before capping the vessel. If no appreciable reaction occurs, a sample weight up to 1 g can be used.
NOTE 3 - Some microwave oven models may be capable of simultaneously processing multiple sample digestion vessels.
10.2.2 Temperature control of closed vessel microwave instruments provides the main feedback control performance mechanism for the test method. Control requires a temperature sensor in one or more vessels during the entire decomposition. The microwave decomposition system should sense the temperature to within +/- 2.5°C and permit adjustment of the microwave output power within 2 s.
10.2.3 All digestion vessels and volumetric ware must be carefully acid washed and rinsed with reagent water. When switching between high concentration and low concentration samples, all digestion vessels (fluoropolymer liners only) should be cleaned by leaching with hot (1:1) hydrochloric acid (greater than 80°C, but less than boiling) for a minimum of 2 h followed with hot (1:1) nitric acid (greater than 80°C, but less than boiling) for a minimum of 2 h and rinsed with reagent water and dried in a clean environment. This cleaning procedure should also be used whenever the prior use of the digestion vessels is unknown or cross contamination from vessels is suspected. Polymeric or glass volumetric ware and storage containers should be cleaned by leaching with more dilute acids (approximately 10 % V/V) appropriate for the specific plastics used and then rinsed with reagent water and dried in a clean environment.
10.2.3.1 Alternate cleaning procedures may be utilized if they are shown to be satisfactory.
10.2.4 The analyst should be aware of the potential for a vigorous reaction. If a vigorous reaction occurs upon the initial addition of reagent or the sample is suspected of containing easily oxidizable materials, allow the sample to predigest in the uncapped digestion vessel. Heat may be added in this step for safety considerations (for example, the rapid release of carbon dioxide from carbonates, easily oxidized organic matter, etc.). Once the initial reaction has ceased, the sample may continue through the digestion procedure.
10.2.5 Seal the vessel according to the manufacturer's directions. Properly place the vessel in the microwave system according to the manufacturer's recommended specifications and connect appropriate temperature and pressure sensors to vessels according to the manufacturer's specifications.
10.2.6 Pressure control for a specific matrix is applicable if instrument conditions are established using temperature control. Because each matrix will have a different reaction profile, performance using temperature control must be developed for every specific matrix type prior to use of the pressure control system. At the end of the microwave program, allow the vessels to cool for a minimum of 5 min before removing them from the microwave system.
10.2.7 Program the microwave oven to heat at 125 W for 15 min, then ramp up to 190 W for another 15 min.
NOTE 4 - Different microwave oven models may require different temperature ramping and holding profiles.
NOTE 5 - Care must be taken to keep internal temperature and pressure within the capability of the vessels used. Excessive heat and pressure will cause the digestion pressure vessels to deform and potentially leak.
10.2.8 Detailed safety recommendations specific to the model and manufacturer of the microwave digestion system is beyond the scope of this test method. The user of this test method is advised to consult the equipment manual, the manufacturer and other literature sources for proper safe operation of the digestion system. The user should be advised that digestion of samples within the scope of this test method could rapidly generate high pressure beyond the mechanical capacity of the vessel, which may cause a rupture of the vessel and damage to the digestion system. (Warning - Exercise caution when handling vessels after they have been heated since they may possess high internal pressures.)
10.2.8.1 Warning - The outer layers of vessels are frequently not as acid or reagent resistant as the liner material and must not be chemically degraded or physically damaged to retain the performance and safety required. Routine examination of the vessel materials may be required to ensure their safe use.
10.2.8.2 Warning - Another safety concern relates to the use of sealed containers without pressure relief devices. Temperature is the important variable controlling the reaction. Pressure is needed to attain elevated temperatures, but must be safely contained. However, many digestion vessels constructed from certain suitably inert polymerics may crack, burst, or explode in the unit under certain pressures. Only suitably inert polymeric (such as PFA or TFM and others) containers with pressure relief mechanisms or containers with suitably inert polymeric liners and pressure reliefmechanisms are considered acceptable. Users are therefore advised not to use domestic (kitchen) type microwave ovens or to use inappropriate sealed containers without pressure relief for microwave acid digestions by this test method. Use of laboratory-grade microwave equipment is required to prevent safety hazards.
10.2.8.3 Warning - Laboratories should not use domestic (kitchen) type microwave ovens for this test method. There are several significant safety issues. First, when an acid such as nitric is used to effect sample digestion in microwave units in sealed vessels equipment, there is the potential for the acid gas vapor released to corrode the safety devices that prevent the microwave magnetron from shutting off when the door is opened. This can result in operator exposure to microwave energy. Use of a system with isolated and corrosion resistant safety devices prevents this from occurring.
10.2.8.4 Warning - Toxic nitrogen oxide(s), hydrogen fluoride, and toxic chlorine (from the addition of hydrochloric acid) fumes are usually produced during digestion. Therefore, all steps involving open or the opening of microwave vessels must be performed in a properly operating fume ventilation system.
10.2.8.5 Warning - The analyst should wear protective gloves and face protection and must not at any time permit a solution containing acid to come in contact with skin or lungs.
10.2.9 After the heating cycle is complete, place the heating pressure vessels in an ice bath for at least an hour to cool. Quantitatively transfer the dissolved sample into a 25 mL volumetric flask and bring it up to volume with deionized water. (Also, see Note 1.)
NOTE 6 - Care must be exercised when opening the pressure vessel so that the contents do not spill out.
NOTE 7 - There may be some insoluble residue at the end ofdissolution steps above if the grease sample contains refractory elements such as silicon, molybdenum, barium, etc. In such cases use of hydrofluoric acid to dissolve the residue may be required. If HF is used, HF-resistant labware must be used during the dissolution steps. Also, an HF-resistant ICP sample introduction system should be used if silicon is to be quantified and to minimize potential damage to the "solution wetted" glass components in the ICP. Some post-digestion organic residue may also remain in the microwave digestion vessels and seals. They can be identified as floating immiscible organic residue or "ring" around the liquid level of the microwave digestion vessel, most likely leached of any analyte and not containing any metals.
11. Preparation of ICPAES Instrument
11.1 Instrument - Design differences between instruments, ICP excitation sources, and different selected analytical wavelengths for individual spectrometers make it impractical to detail the operating conditions. Consult the manufacturer's instructions for operating the instrument.
11.2 Peristaltic Pump - If a peristaltic pump is used, inspect the pump tubing and replace it, if necessary, before starting each day. Verify the solution uptake rate and adjust it to the desired rate.
11.3 ICP Excitation Source - Initiate the plasma source at least 30 min before performing an analysis. During this warm up period, nebulize either water or a dilute (5 %) acid solution.
NOTE 8 - Some instrument manufacturers recommend even longer warm-up periods to minimize changes in the slopes of calibration curves.
11.4 Wavelength Profiling - Perform any wavelength profiling that is specified in the normal operation of the instrument.
11.5 Operating Parameters - Assign the appropriate operating parameters to the instrument task file so that the desired elements can be determined. Parameters to be included are element, wavelength(s), background correction points (optional), interelement correction factors (see 6.1), and integration time. Multiple integrations (typically three) are required for each measurement. A typical measurement time is 10 s.
NOTE 9 - Typical ICP operating conditions follow. Different conditions specific to different instruments may be used.
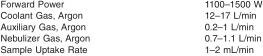
12. Preparation of Calibration Standards
12.1 Blank - Prepare a blank solution by adding same concentration of diluted acids as used in the sample dissolution (usually 5 % nitric acid).
12.2 Working Standards - Prepare by diluting stock standard solutions (see 8.6) to appropriate levels, usually 1 to 10 mg/L concentration with dilute nitric acid solution.
12.3 Check Standards - Prepare instrument check standards in the same manner as working standards such that the concentration of the elements in the check standards are similar to the concentration of elements in the test specimen solutions.
12.4 Internal Standard Stock Solutions (Optional):
12.4.1 The analyst's selection of the single element internal standard may be influenced by the capabilities (wavelength availability, sensitivity) of the ICP-AES instrument available. The single element chosen as the internal standard should not be a component of the grease test specimen or calibration standard. Table 3 lists some commonly used internal standards, their recommended wavelengths, and their approximate concentration for use in this test method.
12.4.2 Prepare a stock solution of the internal standard by weight from a 500 mg/kg single element standard material with appropriate dilution with dilute acid solution. Prepare a concentration that is approximately 50 times the concentration required in the grease test specimen and working standard. Prepare fresh internal standard stock solution weekly.