ASTM D7169 Standard Test Method for Boiling Point Distribution of Samples with Residues Such as Crude Oils and Atmospheric and Vacuum Residues by High Temperature Gas Chromatography
6. Apparatus
6.1 Gas Chromatograph - A gas chromatograph provided with a cryogenic valve for cooling the oven to sub ambient temperatures is required. The conditions of operating the Gas Chromatograph are given in Table 1. It shall also have the following components:
6.1.1 Flame Ionization Detector (FID) - A flame ionization detector capable of maintaining a temperature 5 to 10°C higher than the highest column temperature. The flame ionization detector should possess a jet orifice of about 0.018 in. (0.45 mm) in order to delay the plugging of the orifice due to column bleed. The FID should possess a sensitivity of 0.005 coulombs/g (see Practice E594) and should have a linear range of 106.
6.1.2 Inlet - Either a temperature programmable inlet with a glass liner or a cool-on-column inlet can be used. The inlet shall be capable of operating in a temperature-programmed mode from 50°C to the final temperature of the oven. It is important that the temperature of the inlet, at any time during the analysis, be either equal to or greater than the oven temperature. With the use of either inlet, frequent replacement of the liner or removal of a section of the column may be required due to accumulation of non-volatile sample components. It is important that a leak free seal be reestablished after replacement of the liner or the removal of a small section of the column.
6.2 Carrier Gas Purification System - Gas purifiers are used in order to remove traces of oxygen as well as moisture and other impurities present in the carrier gas. The purification system should contain a hydrocarbon trap and an oxygen trap. The latter should preferably have a visible indicator in order to assess the remaining capacity of the oxygen trap.
6.3 Data System - A data system composed of a computer and software for data acquisition, which digitizes the detector signal, is recommended. Some instrumentation digitizes the signal at the electrometer board in order to reduce noise. The data system is used at acquisition rates of about 10 Hz, which correspond to slices of 0.1 s. This rate of data acquisition is necessary to obtain a minimum number of slices void of sample or solvent elution immediately after injection. Data acquisition systems facilitate the inspection of the baseline under high magnification and allow the inspection of the retention time calibration mixture chromatogram. Retention time shifts can be measured. Overlaying chromatograms is also possible to ascertain similar signal amplitude.
6.4 Integrator - An integrator that digitizes the signal can also be used to acquire chromatograms of the retention time calibration mixture, the sample, the solvent and the reference oil standard.
6.5 Automatic Sample Injector - It is mandatory to use an auto sampler since the external standard technique used in this analysis requires identical volumes for all injections. Additionally, small volumes (0.1 to 0.2 µL) shall be injected in a reproducible manner. Syringes of 5 to 10 µL having needle gauges of size 23 to 26 are to be used.
6.6 Carrier Gas Control - The gas chromatograph shall be operated under constant flow conditions. The flow rate at the beginning of the oven temperature program shall not differ by more than 1 % from the flow measured at the final oven temperature. Electronic pneumatic control is highly recommended.
7. Column and Column Performance Criteria
7.1 A 100 % bonded polydimethylsiloxane column having a nominal inside diameter of 0.5 mm and a film thickness of 0.09 to 0.17 µm is used.
7.2 The column used should be capable of sustaining temperatures of 435°C under temperature programming. Aluminum covered fused silica and metal columns have been successfully used.
7.3 The column should be capable of eluting carbon number 100 at its highest temperature. It is important that C100 be eluted during the temperature program cycle of the oven.
7.4 Column resolution is determined from the separation of carbons 50 and 52 in the retention time calibration mixture chromatogram. The resolution should be between 1.8 to 4.0. See Eq 1 in 13.1.
7.5 The column shall be capable of allowing the start of the elution of n-C5 prior to the solvent elution, which is CS2, at -20°C. The descending edge of the n-C5 peak co-elutes with the solvent. It is to be noted that at these low temperatures liquid phases may turn solid, and retention shifts may be observed during the elution of compounds at these low oven temperatures.
7.6 Column Overloading - The prevention of column overloading is carried out by determining the skewness of a selected peak among the components of the retention time calibration mixture chromatogram. Any paraffin with a carbon number between C12 and C24 may be chosen. The skewness should be between 0.8 to 1.2. See Eq 2 in 13.2.
7.7 Column Flow - Helium is used as carrier. Column flow rate is set to 20 mL/min.
8. Reagents and Materials
8.1 Carbon Disulfide (CS2), 99+ % pure. (Warning - Extremely flammable and toxic liquid.) Used as a solvent to dilute the sample and standards as well.
8.2 Polywax 655 or Polywax 1000 - Used as a component of the retention time calibration mixture. Since these Polywaxes have carbon 22 as the first component, it shall be complemented with the mixture of paraffins described in 8.4.1 and 8.4.3 so that the entire range of carbon numbers (C5-C100) is present in the sample.
8.3 Paraffins - The following normal paraffins are used in the preparation of the retention time calibration mixture:
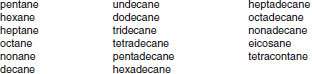
8.3.1 The purities of these compounds should be 99 % or greater.
8.4 Retention Time Calibration Standard - This standard can be obtained from chromatography supply companies. This standard is composed of a mixture of Polywax (either P655 or P1000) as well as a mixture of paraffins. The addition of the paraffin mixture is necessary to cover the range of C5-C20 since these paraffins are absent in the Polywax. Furthermore the amounts of the paraffins are chosen so as to facilitate identifying the carbons in the retention time calibration mixture chromatogram. Alternatively, a successful mixture that has been used may be prepared by the procedure described in 8.4.1-8.4.3 which requires the preparation first of the n-paraffin mixture (see 8.3) and then spiking an aliquot of this mix to a weighed amount of Polywax 655 or 1000.
8.4.1 Place approximately 20 mL of CS2 into a round bottom 50 mL flask. Transfer with care.
8.4.2 Prepare a mixture of the paraffins listed in 8.3 as follows. Weigh 500 mg of each component into a 20 mL vial. Add an additional 500 mg for dodecane and about 20 mg of tetracontane. Store this mixture at 4°C and use it as a spiking mixture in the preparation of the Polywax 655 retention time calibration mixture.
8.4.3 Weigh about 25 mg of the Polywax 655 and add it to the vessel prepared in 8.4.1. Add approximately 10 mg of the paraffin spiking mixture prepared in 8.4.2. Stir the solution under a fume hood and heat with an infrared lamp (about 200 watts) placed at a safe distance (about 15 to 20 cm) from the mixture for a period of 20 min or until the solution is clear. Other precautionary methods of dissolution are acceptable. Careful attention should be given to avoid the ignition of the CS2 (see 8.1).
8.4.4 Transfer a 2 mL aliquot of the final mixture obtained in 8.4.3 into a 2 mL auto sampler vial and seal it firmly. This solution can be used for about one week if stored at 4°C. The contents of this vial are injected in order to obtain the retention time–boiling point curve.
NOTE 1 - Polywax is a trademark of the Baker Petrolite Corporation (Barnsdall, OK). This retention time calibration mixture is commercially available from chromatographic supply houses as well as from companies that build simulated distillation analyzers. The retention time calibration mixture may differ among supply houses in that docosane, tetracosane and hexacosane are also added to the Polywax 655 or Polywax 1000 in order to enhance the concentration of these hydrocarbons in the polywaxes.
8.5 Detector Relative Response Test Mixture - It is necessary to initially validate the response of the entire gas chromatographic system. Since this test method assumes that all hydrocarbons have the same relative response regardless of their retention time, a solution shall be prepared in order to determine the relative response factors.
8.5.1 Prepare a solution containing the following normal paraffins:

8.5.2 Weigh about 100 mg of each paraffin to the nearest 0.1 mg into a 50 mL volumetric flask. Mix well and add CS2 to the mark. Ensure that the paraffins are completely dissolved. Record the masses of the paraffins, which will be used in Eq 3 in order to calculate the relative response factor of each of the paraffins.
8.5.3 Record the assayed purity of each paraffin for use in Eq 3.
8.5.4 Transfer an aliquot of the mixture prepared in 8.5.2 to a 2 mL injection vial. Ensure that the components are in solution prior to the transfer. Warm the vial if necessary. Inject 0.1 to 0.2 µL.
8.6 Reference Oil 5010 - In order to determine the sample recovery, the detector response factor has to be determined. For this purpose, utilize Reference Oil 5010 as an external standard. This material is obtainable from various chromatography suppliers.
8.7 Gases - The following compressed gases are utilized for the operation of the gas chromatograph:
8.7.1 Nitrogen, 99.999 %. (Warning - Compressed gas under high pressure.) Total impurities should not exceed 10 mL/m3. This gas is used as detector makeup. Helium may be used as makeup gas.
8.7.2 Hydrogen, 99.999 %. (Warning - Extremely flammable gas under high pressure.) Total impurities should not exceed 10 mL/m3. This gas is used as fuel for the operation of the detector.
8.7.3 Air, 99.999 %. (Warning - Compressed gas under high pressure and supports combustion.) Total impurities should not exceed 10 mL/m3. This gas is used to sustain combustion in the FID detector.
8.7.4 Helium, 99.999 %. (Warning - Compressed gas under high pressure.) This gas is used as carrier gas and should not contain more than 5 mL/m3 of O2. The total amount of impurities should not exceed 10 mL/m3.