11. Test Procedure
11.1 Pre-Test, Start, and Motoring Phase:
11.1.1 Installation of Test Unit - Install the assembled test unit on the motoring rig. Connect the driveshaft and temperature probe. Install the cooling fan and heat lamp pair as shown in Fig. A5.3.
11.1.2 Adjust the temperature controller to maintain 180 °F +/- 1 °F (83 °C +/- 0.6 °C).
11.1.3 Start the driving motor and immediately accelerate the motor to 2500 r/min +/- 25 r/min. Record the time and the initial oil temperature at the time of the driving motor start up.
11.1.4 Do not exceed 8 h between the beginnings of the abrasive blasting of axle parts to the start of the motoring phase of the test.
11.1.5 Using a syringe, add 67.5 mL +/- 0.6 mL (2.3 oz +/- 0.02 oz) of specified test water to the test unit through the full port valve within 5 min after starting the drive motor. If using Dana Model 30 hardware rather than the AAM K2XX hardware add 1.00 oz +/- 0.02 oz (29.6 mL +/- 0.6 mL) instead. Connect the pressure relief system.
11.1.6 Monitor oil temperature and when the oil temperature reaches 180 °F +/- 1 °F (83 °C +/- 0.6 °C), close full port ball valve, disconnect the pressure relief system, and plug the downstream side of valve. This prevents escape of any additional water vapor. Measure and record drive pinion r/min and oil temperature, and report the time at the beginning of motoring phase. Allow a 1 h maximum warm up time for the oil to reach operating temperature of 180 °F +/- 1 °F (83 °C +/- 0.6 °C).
11.1.6.1 Occasionally, a small amount of the test oil and water emulsion will foam up from the axle housing into the accumulator during warm-up. Make every effort to allow the test oil and water emulsion to return to the test axle. Stop the motoring and heating of the test unit in an attempt to return the test oil and emulsion to the test axle. There may be occasions when the test oil and water emulsion will not completely drain back into the carrier as the unit reaches operating temperature. Use caution not to exceed the 1 h maximum warm-up time. Report the number of shutdowns and the estimated amount of test oil and water emulsion that did not return to the carrier in the comment section of the test report.
11.1.7 Motor the test unit for 4.0 h +/- 0.1 h at 180 °F +/- 1 °F (83 °C +/- 0.6 °C) and 2500 r/min +/- 25 r/min.
11.1.8 At the end of the motoring phase, measure, and record drive pinion r/min and report the time. Stop the driving motor, turn off the heat lamps and cooling fan.
11.2 Transition Phase:
11.2.1 Move the test unit to the storage box within 30 min of the end of the motoring phase. See Fig. A5.6 for physical position. Set the controller at 125 °F +/- 1 °F (52 °C +/- 0.6 °C). Position the axle such that the axle tube openings and the pinion shaft are on a horizontal plane.
11.2.2 Switch on the internal fan. Activate the control system to maintain a test oil temperature of 125 °F +/- 1 °F (52 °C +/- 0.6 °C). The maximum allowable time for the test oil to reach operating temperature of 125 °F +/- 1 °F (52 °C +/- 0.6 °C) from the end of the motoring phase of the test as stated in 11.1.8 is 1 1/2 h.
11.3 Storage Phase:
11.3.1 Record the time of the first occurrence of the test oil temperature reaching 125 °F +/- 1 °F (52 °C +/- 0.6 °C). This is the start of the storage phase.
11.3.2 Continue the storage phase for a total of 162 h +/- 0.2 h.
11.3.3 At the end of the storage phase, record the time, then switch off the storage box-heating unit and circulating fan. The end of the storage phase is the end of the test.
11.4 Post Test Procedure:
11.4.1 Immediately remove the test unit from the storage box. Disconnect the temperature sensor. Drain and discard the used test oil. Completely disassemble the test axle within 1 h after the test complete as stated in 11.3.3.
11.4.2 Lightly pressure wash all parts with a solvent (see 7.2) to remove used test oil.
11.4.3 Coat test parts in Mobil Arma 245 prior to final rating.
11.4.4 Clean and coat all parts in MobilArma 245 within 1 h after disassembling the test axle.
11.4.5 If the rating is not to be conducted within 24 h of the end of the test, the coated test parts shall either be stored submerged in the preservative oil, or stored as is in airtight, closed containers. Wrapping the test parts in NOX-RUST paper for long-term storage has also been found to be acceptable.
NOTE 2 - To preserve test parts in storage or for shipment after completion of all rating and optional documentation photographs, the rust preventative Mobil Arma 245 has been found to be effective in preventing new rust buildup in post-test ambient storage conditions.
12. Determination of Test Results
12.1 Conduct parts rating within 14 days from the end of test, under lighting conditions described in ASTM Distress Rating Manual 21. Rate parts in accordance to ASTM Distress Rating Manual 21 and Annex A7. The rating procedure described in Annex A7 supersedes that found in ASTM Distress Rating Manual 21 where applicable. Deposits on rated items will fall under one of two categories: (1) Rust or corrosion; (2) Stain and sludge or other.
12.2 Rust or corrosion deposits will be assigned one of the following integer values: 10, 9, 8, 5, or 0, using these definitions:
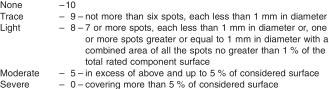
12.3 The areas in Table 1 will be rated as described above.
12.4 By filling in values on the rating sheet and then applying the appropriate weighting values shown in Annex A9, a final deposit merit value is obtained. To maintain comparable test severity to the Dana Model 30 hardware, add 0.6 merits to the final deposit merit value when using AAM K2XX hardware for non-reference oil testing. In instances where this results in a merit value greater than 10, report the result as 10 merits. Note the presence, location, and amount of additional deposits, such as stain and sludge, or other, in the Remarks section on the rating sheet. Also note rust in non-rated areas in the Remarks section.
12.5 For a valid rating, rate the test by an individual who has participated in an ASTM sponsored, high volume gear rater calibration workshop within the previous 12 months.
12.6 Test Validity - The test is determined to be operationally valid if the percent deviation of the critical operating parameters and number of downtimes are within the limits specified and defined in Annex A6.
12.7 Severity Adjustment - Calculate severity adjustments (SA) for results of non-reference gear oil tests. Use the control chart technique, referenced in Annex A8, for determining the laboratory bias for rust or corrosion deposits. Enter the adjustments on the appropriate test form.