6. System Components
6.1 Process analyzers for measuring the chemical composition of aromatic hydrocarbons, their purity, or physical properties often replace existing laboratory test methods, using the same or similar chemical measurement techniques. Fig. 1 shows several possible analyzer configurations for on-line process testing of aromatic hydrocarbon materials. Aromatic hydrocarbon stream analyzers are often based on chromatography, but they may also perform physical measurements, wet chemistry, or other methods described in new or existing Committee D16 methods. This practice is intended to be generally applicable to any of them.
7. Performance Guidelines Before Calibration
7.1 At startup, validate any process analyzer against an existing analytical method, typically in this case, one overseen by Committee D16.
7.2 The capability measurement (cm) for a given analyzer (3) shall be less than 0.2, as defined in Eq 1:
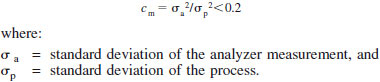
The variance (standard deviation squared) of the analyzer should be less than 20 % of the variance of the process, so that the analyzer measurement can be useful for detecting changes in the process. The expected capability for a process analyzer measurement may be available from the vendor for a specific application before installation of the analyzer (advertised analyzer capability). Actual process stream measurement capability should be measured on the process/product stream, usually after initial analyzer validation.
7.3 Automated analyzer sampling practices for aromatic hydrocarbon liquid streams shall follow those referenced in Practice D4177.
7.4 Determine the linearity of the process analyzer by using at least three calibration standard materials with known compositions/responses for the components of interest. Each component should be present at a high, low, and medium concentration/amount level with respect to the concentration/amount range expected for the parameter (analyzer operating range). A plot of the component concentration/amount versus analyzer response will determine if the analyzer has a linear response over the concentration range of interest. If analyzer response is nonlinear, additional calibration standards must be analyzed to clearly determine the nonlinear behavior of each analyzer and component, if the analyzer is to be used in the nonlinear range.
7.5 If a process analyzer is to be used only for trend information, the data generated by it is in a form that does not impart compositional information, but relative information only, that is, peak area, peak height, counts, millivolts, etc. Initial validation and frequent performance testing are still required to define precision, as well as to maintain proper analyzer operation.
8. Performance Test Procedure
8.1 Determine analyzer performance using external check samples, which are substituted for the process material stream during performance test runs.
8.2 Process analyzers are routinely performance tested by using control samples. These may be primary or secondary standard materials, or actual portions from the process stream. These portions must be representative of normal process conditions, and be stored to remain physically and chemically stable over time. The control sample should be repeatedly analyzed by the process analyzer, and then using statistical process control (SPC), to define the actual analyzer result's precision.
8.3 Analyzer performance test frequency can be done at a fixed time interval, based on analyzer reliability and operator experience. Typically, once per shift, day, or week are used, but it may be more or less frequent. Unscheduled control sample analyses may be performed whenever the unit operator feels that something has changed in the process or process analyzer, or at a convenient time.
8.4 The control sample material container shall be located at a point in the process to allow for its simple and regular introduction into the process analyzer's sample introduction system (if appropriate) by the process operator. A sufficient quantity must be available for many repetitive analyses.
8.5 Perform an external analyzer performance test by switching the analyzer sample source from the process stream to the control sample, followed by sampling and analysis of the control sample.
8.6 Monitor the analyzer's output from the control sample until it stabilizes, that is, the difference between successive readings is at or below the repeatability of the analyzer, (which is measured as described in 8.10). If this does not occur, the repeatability of the analyzer has changed and should be remeasured.
8.7 After stabilization of the analyzer, measure at least three successive results on the control sample and average the results. Plot the average of these three results in a SPC chart using any statistically correct method of data handling and control chart construction (4).
8.8 SPC charts of the control sample data shall be used to help decide if the analyzer needs to have its response parameters reset, (5) or if it is working within previous statistical levels and should be left alone. SPC results and operator experience should be used to determine subsequent actions, such as determining the cause for any rule violation and correcting it.
8.9 SPC charts of control samples help the operator to differentiate between normal (random) and abnormal (nonrandom) analyzer variation due to changes in analyzer operation. 8.9.1 Charts may be maintained manually or with commercially available SPC software, preferably as part of the analyzer data acquisition and control software.
8.9.2 Control limits should be set at three (3) sigma (standard deviations) from the mean value, warning limits at two (2) sigma, and suitable Western Electric rules (2) invoked, consistent with plant/facility statistical policy.
8.9.3 All rule violations shall be investigated and eliminated if possible, with all causes and actions documented with the charts.
8.9.4 If a cause cannot be determined, analyzer operation should continue without any parameter adjustment until the next performance test.
8.9.5 If there are no rule violations, analyzer parameter adjustment is not needed.
8.9.6 If a rule violation's cause is determined and eliminated, and if the operator feels that the analyzer's accuracy has changed as a result, proceed to reset analyzer parameters, as discussed in Section 9. If precision needs to be redefined for the analysis process, follow the procedure listed in 8.10.
8.10 To determine the repeatability of the analyzer, follow the following procedure:
8.10.1 Switch a control sample into the analyzer and wait for stabilization as discussed in 8.6.
8.10.2 Measure at least eleven (6) successive analyses on the control sample over at least 1 h or reasonable interval on the same day. The control sample should be switched into and out of the analyzer stream for each determination.
8.10.3 The 95 % repeatability limit of the measurement for the analyzer equals the standard deviation of these 11 successive runs multiplied by 2.8, in accordance with Terminology E456.
8.10.4 Recalculate the analyzer's control limits based on this new set of data, and reset the SPC chart's parameters. Continue to collect data for subsequent performance tests, and reevaluate the SPC chart control limits after 20 additional points have been collected.
8.10.5 Repeatability should be measured any time the analyzer's precision is suspected to have significantly changed, as indicated by the control sample SPC chart, or if the analyzer's response variation is excessive after an analyzer stream change. An indication of analyzer precision should always be made available to persons receiving data from the analyzer. Any large changes in an analyzer's precision should immediately be brought to the attention of the user of the analyzer's data.
8.11 Perform periodic analyzer validation on a scheduled basis over a longer time (for example, weekly or monthly) than performance testing, or whenever some significant aspect of the analyzer has changed (see Table 1). This activity reestablishes the analyzer's statistical performance with the primary method.