11. Procedure
11.1 Measure the initial acid number of the oils to be tested by Test Method D664, D3339, or D974 and the initial viscosity at 40°C by Test Method D445.
11.2 Adjust the heating block to a temperature high enough to maintain the oil in the oxidation test cell at 155 +/- 0.5°C. The 155 +/- 0.5° setting is predetermined with a calibrated thermometer or thermocouple sitting on the bottom of a test cell containing 100 g test fluid with 3.0 +/- 0.5 L/h dry air flowing through the fluid.
11.3 Place the catalyst coil and gas inlet tube in the test cell. Obtain the total weight, W1, of these three components to the nearest 0.1 mg. The components may be weighed either separately or together.
11.4 Remove the gas inlet tube and weigh 100 +/- 1 g of test fluid into the oxidation test cell.
11.5 Fit the gas inlet tube and basic head into the test cell so that the tip of the gas inlet tube rests on the bottom of the test cell inside the catalyst coil. A PTFE sleeve may be used when inserting the basic condenser head into the cell. No grease is to be used in the ground glass joint.
11.6 Place the test cell into the preheated constant temperature block.
11.7 Connect a gas delivery tube from the flow control system to the gas inlet tube and adjust the flowmeter control to deliver dry air at 3 +/- 0.5 l/h. Record this time as the start of the test.
11.8 Recheck the air flow and temperature after the test is underway and at least once daily during the test. Adjust to maintain the air flow and temperature as needed.
NOTE 3 - Exhaust gases need not be collected. Vent exhaust gases properly.
11.9 After 96 h, shut off the temperature and air flow. Remove the gas inlet tube supporting the catalyst coil and remove the test cell from the heating block. Wash gas inlet tube with sufficient heptane to remove all test fluid and set it aside in a clean location.
11.10 Allow sample to cool for a minimum of 16 but no longer than 72 h.
11.11 Dry a No. 41 Whatman filter and an 8 µm filter membrane in an oven at 70°C for 1 h and cool in a desiccator. Using weighing vessel, obtain the weight of the No. 41 Whatman filter, W2, and the 8 µm filter membrane, W3, each to the nearest 0.1 mg.
11.12 Filter the oil first through the preweighed No. 41 Whatman filter paper and then in a separate filtration apparatus through the 8 µm membrane filter. Transfer the filtrate into a clean 250 mL beaker and set aside for acid number and viscosity determinations.
11.13 Reassemble the Whatman filtration apparatus. Rinse the oxidation cell plus catalyst coil with sufficient 100 mL portions of heptane to ensure complete transfer of loose insolubles to the Whatman filter and removal of all test fluid from the test cell. Do not attempt to dislodge insolubles from the coil, gas inlet tube, or oxidation tube.
11.14 Rinse both filters with sufficient heptane till the fluid passing through the filters is completely colorless. With the vacuum applied, remove the clamp and funnel from the filter membrane and funnel base. Rinse the surface of the membrane with a gentle stream of heptane, directing the stream from the edge towards the center so as to remove final traces of oil from the membrane. Maintain the vacuum for a short time to remove final traces of heptane. Transfer the membranes to the identical weighing vessels used in the initial weighing and dry for at least 1 h in the oven at 105°C. Allow to cool for at least 1 h and determine the weights of the No. 41 Whatman filter, W2a, and the 8 µm filter membrane, W3a, to the nearest 0.1 mg.
11.15 Dry the test cell plus gas delivery tube plus catalyst coil in an oven at 70°C for at least 1 h. Allow to cool for at least 1 h and determine the combined weight of these three components, W1a.
11.16 Determine the acid number of the oxidized oil filtrate according to the same procedure used in 11.1.
11.17 Determine the viscosity of the oxidized oil filtrate at 40°C according to Test Method D445.
11.18 Compare test cell appearance to the ASTM Oxidation Cell Varnish Standards (ADJD6514). Hold both the cell and the standard in such a manner that light reflected from them at an angle of approximately 45° will be observed.
12. Calculations
12.1 Total weight of insoluble material:
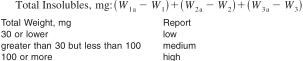
12.2 Change in Acid Number (AN):
Change in AN = ANf - ANi
where:
ANf = final AN.
ANi = initial AN.
12.3 Percent Increase in Viscosity at 40°C:
% Increase in Viscosity @ 40°C (Vf - Vi)/Vi x 100
where:
Vf = final viscosity.
Vi = initial viscosity.
13. Interpretation
13.1 Interpret the oxidation stabilization of the sample accordingly as the appearance of the oxidation cell agrees with one of the varnishes of the ASTM Oxidation Cell Varnish Standard (ADJD6514).
13.1.1 When the appearance of the oxidation cell is in the obvious transition state between that indicated by any two adjacent standard varnishes, judge the sample by the more varnished standard color.