ASTM D6421 Standard Test Method for Evaluating Automotive Spark-Ignition Engine Fuel for Electronic Port Fuel Injector Fouling by Bench Procedure
8. Preparation of Apparatus
8.1 Fuel Injector Preparation:
8.1.1 The injectors shall be cleaned (see A3.2) prior to the running of the test. Proper cleaning is essential for running a valid test.
8.1.2 Check the injector flow (see A3.5). Injectors shall meet the conditions of Annex A4 before beginning the test.
8.2 Place the injectors into the fuel handling unit (see A3.3).
8.3 Pressurize the tank and the fuel lines with nitrogen gas.
8.4 Set test parameters as specified in Table 1. If using a programmable controller, program the controller in accordance with A3.4, or refer to your manufacturer's manual.
8.4.1 The test will run for 44 cycles with measurements taken at the end of each 22-cycle segment.
8.5 Add fuel to the internal fuel reservoir (see A3.5).
9. Procedure
9.1 Mount screened and cleaned injectors into the fuel handling unit and fasten in place (see A3.3).
9.2 Ensure that test parameters are set in accordance with Table 1 and that all other steps in Section 8 have been completed.
9.3 Measure the initial, or pre-test injector flow (see A3.6).
9.3.1 Prior to making the measurement, bleed off any gases in the fuel rail (see A3.6) and discard the fuel.
9.3.2 Measure the flow masses for the four injectors independently. Hold the injector pintle open for 12 s while subjecting fuel to an initial nitrogen pressure of 263 kPa (see 6.1.3).
9.3.3 Record and average three separate flow mass measurements for each injector.
9.4 Begin test.
9.5 After completing 22 cycles, allow the base (aluminum block) temperature to cool to 24 +/- 3°C (75 +/- 5°F). The flow measurement (see A3.6) shall be performed within 4 h of completing 22 cycles and with the same test fuel used for the pretest flow. Record flow measurement results (see A3.6) and the base temperature at which the flow measurements were generated.
9.6 The test may be aborted at this point if the test parameters detailed in 10.4 have been compromised, or if any equipment malfunction has been detected. Otherwise, continue testing for an additional 22 cycles.
9.7 After 44 cycles have been completed, allow the base temperature to cool to 24 +/- 3°C (75 +/- 5°F). Perform the flow measurement within 4 h of test completion and with the same test fuel as used for the pretest flow. Record flow measurement results (see A3.6) and the base temperature at which the flow measurements were generated.
10. Calculation
10.1 Number of Test Cycles - Complete 44 test cycles. Break the 44 cycles into two groups of 22 cycles run consecutively, with a break in between of less than 4 h.
10.2 Fuel Injector Flow Measurement - Statically flow test (see A3.6) injectors while still in the apparatus for 12 +/- 0.5 s, using the test fuel. To ensure that the test fuel completely fills the injector during flow testing, flush injectors for at least 10 s with the test fuel prior to the start of the flow testing.
10.3 Calculation of Fuel Injector Fouling - Express the amount of fuel injector fouling as the percent difference between the 12 s flow mass of the cleaned injector and the 12 s flow mass of the same injector during or after the test period. Calculate fuel injector fouling using the following equation:
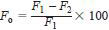
where:
Fo = percent fouling,
F1 = initial flow mass to nearest tenth gram, and
F2 = flow mass at end of test to nearest tenth gram.
For each injector, calculate the percent fouling of each of the three flow mass readings, and report the average. Take the average of the four injectors and report to the nearest percentage point.
10.4 Determination of Test Validity - During each test, strictly adhere to and monitor conditions of the bench test apparatus. As a minimum, record the following data while the apparatus is running: (a) the fuel rail pressure, (b) the manifold (aluminum block) temperature, and (c) the time of each portion of the test cycle (pulse, heating, cool down).
10.4.1 Fuel Rail Pressure - In a graphical representation of the pressure in the fuel rail, show that the pressure is maintained through the 60 min soak period at 263 +/-7 kPa (38 +/-1 psi).
10.4.2 Manifold Temperature - In a graphical representation of the temperature of the manifold (aluminum block), show that the temperature of the manifold is maintained at 160 +/- 5°C (320 +/- 9°F) for a minimum of 40 min of each cycle.
10.4.3 Test Timing - Use a timer, accurate to 0.1 s to verify that the pulse time of the injectors is 15 +/- 1 s.