6. Apparatus
6.1 Manual Apparatus:
6.1.1 The apparatus, as detailed in 6.1.2-6.1.13, shall be arranged as shown in Fig. 1.
6.1.2 Test Jar, cylindrical, of clear glass, flat bottomed, with an internal diameter of 31.5 more or less 0.5 mm, a wall thickness of 1.25 more or less 0.25 mm and a height of 120 more or less 5 mm. The jar shall have a permanent mark at the 45 more or less 1 mL level.
NOTE 2 - Test jars of the required dimensions may be obtained by selection from jars conforming to Test Method D2500, which specifies a wider diameter tolerance.
6.1.3 Jacket, brass, watertight, cylindrical, flat bottomed, to be used as an air bath. It shall have an inside diameter of 45 more or less 0.25 mm, outside diameter of 48 more or less 0.25 mm, and a height of 115 more or less 3 mm (see Fig. 2).
6.1.4 Insulating Ring, made from oil-resistant plastics or other suitable material, to be placed in the bottom of the jacket (see 6.1.3) to provide insulation for the bottom of the test jar. It shall fit closely inside the jacket and have a thickness of 6 + 0.3 - 0.0 mm.
6.1.5 Spacers (two), approximately 5-mm thick, made of oil-resistant plastics or other suitable material, to be placed as shown in Fig. 1 around the test jar (see 6.1.2) to provide insulation for the test jar from the sides of the jacket. The spacers shall fit closely to the test jar and closely inside the jacket. The use of incomplete rings, each with a 2-mm circumferential gap, will accommodate variations in test jar diameter. The spacers and insulating ring may be made as a single part as shown in Fig. 3.
6.1.6 Supporting Ring, of oil resistant plastics or other suitable non-metallic, non-absorbent, oil-resistant material, used to suspend the jacket (see 6.1.3) in a stable and upright position in the cooling bath and to provide a concentric location for the stopper (see 6.1.7). A design is shown in Fig. 4 for guidance, but this design may be modified to suit the cooling bath.
6.1.7 Stopper, of oil-resistant plastics or other suitable non-metallic, non-absorbent, oil-resistant material, to fit the test jar and the support ring as shown in Fig. 5. It shall have three holes to accommodate the pipet (see 6.1.8) and the thermometer (see 6.1.9) and to allow venting of the system. If necessary, when using the high-range thermometer (see 6.1.9), the upper part of the stopper shall have an indentation to permit the thermometer (see 6.1.9 (a)) to be read down to a temperature of -30°C. A pointer shall be fitted to the upper surface of the stopper to facilitate location of the thermometer in relation to the bottom of the test jar. A spring wire clip shall be used to retain the thermometer in the correct position.
6.1.8 Pipet with Filter Unit:
6.1.8.1 A Pipet, of clear glass with a calibration mark corresponding to a contained volume of 20 more or less 0.2 mL at a point 149 more or less 0.5 mm from the bottom of the pipet (see Fig. 6). It shall be connected to the filter unit (see 6.1.8.2).
6.1.8.2 A Filter Unit (see Fig. 7), containing the following elements:
(a) A Brass Body, with a threaded cavity that houses the wire mesh holder. The cavity shall be fitted with an O-ring of oil-resistant plastics. The internal diameter of the central tube shall be 4 more or less 0.1 mm;
(b) A Brass Screw Cap, to connect the upper part of the body of the filter unit (see 6.1.8.2) to the lower part of the pipet (see 6.1.8.1) to ensure a leak-free joint. An example of satisfactory connection is shown in Fig. 7.
(c) A Disc, 15 more or less 0.1-mm diameter, of plain weave stainless steel wire mesh gauze with a nominal aperture size of 45 µm. The nominal diameter of the wire shall be 32 µm, and the tolerance for the size of an individual aperture shall be as follows:
(1) No aperture size shall exceed the nominal size by more than 22 µm;
(2) The average aperture size shall be within 6 3.1 µm of the nominal size;
(3) Not more than 6 % of the apertures shall be above the nominal size by more than 13 µm.
NOTE 3 - The requirements for the wire mesh are taken from ISO 3310, to which reference may be made for methods for testing the gauze.
(d) A Filter Holder of Brass, in which the disc of wire mesh gauze (see 6.1.8.2 (c)) is firmly clamped by a retaining ring pressed into the filter holder. The diameter of the exposed part of the gauze shall be 12 + 0.1 - 0.0 mm (see Fig. 8);
(e) A Brass Cylinder, threaded on the outside, that can be screwed into the cavity of the body (see 6.1.8.2 (a)) to clamp the filter holder (see 6.1.8.2 (d)) against the O-ring (6.1.8.2 (a)), The lower end shall have four slots to allow the specimen to flow into the filter unit.
6.1.9 Thermometers, having ranges shown below and conforming to the requirements prescribed in Specification E 1 or Specifications for IP Standard Thermometers.
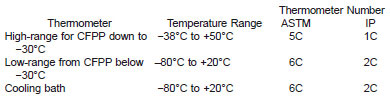
6.1.10 Cooling Bath:
6.1.10.1 The type of cooling bath is optional, but it shall be of a shape and size suitable for containing the jacket (see 6.1.3) in a stable and upright position at the required depth.
6.1.10.2 The bath shall be fitted with a cover with one or more holes in it to accommodate the supporting ring (see 6.1.6). The jacket (see 6.1.3) may be permanently mounted in the cover.
6.1.10.3 The bath temperature shall be maintained at the required value and tolerance by a refrigeration unit or by the use of suitable freezing mixtures, ensuring a homogenous temperature in the bath by stirring or other means of agitation. Table 1 lists the bath temperature set-points required in the CFPP procedure. If only one bath is utilized, it must have the ability to change down to the next lower set-point temperature in a time period not exceeding 2 min 30 s.
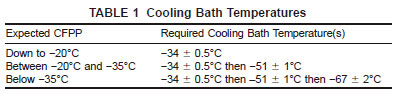
6.1.11 Stopcock, glass, with double oblique bore of 3-mm diameter.
6.1.12 Vacuum Source, vacuum pump or water pump powerful enough to ensure an air flow rate in the vacuum regulator of 15 more or less 1 L/h for the duration of the test.
6.1.13 Vacuum Regulator, consisting of a glass bottle, at least 350-mm high, not less than 5 L capacity, partially filled with water. It shall be closed by a stopper with three holes of convenient diameters for glass tubes. Two tubes shall be short and shall not go below the water level. The third tube, with an internal diameter of 10 more or less 1 mm, shall be long enough for one end to be approximately 200 mm beneath the surface of the water while the other end reaches a few centimetres above the stopper. The depth of the immersed part shall then be adjusted to obtain a depression of 200 more or less 1 mm of water (2 more or less 0.05 kPa) on the manometer, which shall contain water. A second empty 5 L bottle shall be fitted in the line to serve as a vacuum reservoir to ensure a constant depression. The arrangement is shown in Fig. 1.
6.1.14 Stopwatch, with a graduation or reading of 0.2 s or lower, with an accuracy of 0.1 % over a period of 10 min.
6.2 Automated Apparatus:
6.2.1 The automated apparatus shall include elements conforming to 6.1.1-6.1.8, platinum resistance thermometers, cooling bath(s), vacuum pump, and suitable electronic control and measurement devices.
6.2.2 Cooling Bath, a refrigeration unit capable of maintaining the cooling bath at the required temperature and also of automatically changing the bath temperature within 2 min 30 s at the appropriate stage (see 12.2.5).
6.2.3 Vacuum Pump, powerful enough to ensure an air flow rate in the vacuum regulator of a minimum of 15 more or less 1 L/h, and to maintain a constant vacuum of 200 more or less 1 mm (2 more or less 0.05 kPa) for the duration of the test. For multi-position testers using the same vacuum pump, the flow rate shall be checked when several positions are operating simultaneously.
7. Reagents and Materials
7.1 Heptane, clean commercial or reagent grade.
NOTE 4 - Warning: Flammable. Harmful if inhaled.
7.2 Acetone, clean commercial or reagent grade.
NOTE 5 - Warning: Extremely flammable.
7.3 Lintless Filter Paper, (5 more or less 1 µm retention).
7.4 Certified Reference Materials.