6. Apparatus
6.1 Mold - A mold suitable for forming two 1/2 in. (12.7 mm) cubes of pitch, having cylindrical core pins 12 gauge (2.05 mm) in diameter located in the base plate of the assembly to produce accurately centered suspension holes in the cubes. (See Fig. 1.)
6.2 Hooks - Two L-shaped hooks, made of 12 gauge (2.05 mm) copper wire. The foot of the hook shall be 1 in. (25 mm) long and at a right angle to the upright portion for insertion into the center hole of the pitch cube.
6.3 Container - A glass vessel that can be heated, not less than 85 mm in diameter and 105 mm deep. (A standard 600 mL low-form beaker meets these requirements).
6.4 Temperature Measuring Device - Use either a calibrated DCT meeting the requirements described in 6.4.1 or liquid-in-glass thermometers described in 6.4.2. A DCT or calibrated liquid-in-glass thermometer shall be used as the thermometer for temperature measurement independent of the instrument's temperature control, and shall be located in the thermowell.
NOTE 2 - The display device and sensor must be correctly paired. Incorrect pairing will result in temperature measurement errors and possibly irreversible damage to the electronics of the display.
6.4.1 Digital Contact Thermometer Requirements:
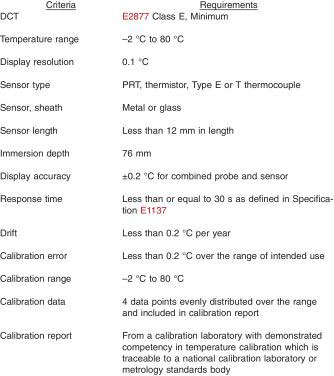
6.4.1.1 The DCT calibration drift shall be checked at least annually by either measuring the ice point or against a reference thermometer in a constant temperature bath at the prescribed immersion depth to ensure compliance with 6.4.1. With respect to an ice bath, Practice E563 provides guidance on the preparation and use of an ice bath. However, for this use, variance from the specific steps, such as water source, is permitted provided preparation is consistent. The basis for the variance is due to the ice bath reference being used for tracking change in calibration not verification.
NOTE 3 - When a DCT's calibration drifts in one direction over several calibration checks, that is, ice point, it may be an indication of deterioration of the DCT.
6.4.2 An ASTM Low Softening Point Thermometer having a range from -2 °C to 80 °C and conforming to the requirements for Thermometer 15 as described in Specification E1 or E2251.
6.4.2.1 Calibration Check - Verify thermometer at least annually against a reference thermometer in a constant temperature bath or an ice bath. The thermometer is to be inserted to its immersion depth. If using an ice bath, the ice point reading is to be taken within 60 min after the thermometer has been at test temperature for at least 3 min. If the corrected temperature reading deviates from the reference thermometer or the ice point, then repeat this calibration check. If the thermometer deviates from the reference value on two successive checks, then a full thermometer recalibration is needed.
6.4.2.2 Recalibration - A complete recalibration of the liquid-in-glass thermometer, while permitted, is not necessary in order to meet the accuracy ascribed to liquid-in-glass thermometer's design until the thermometers corrected measured temperature deviates from the reference thermometer or ice point by one scale division, or until five years has elapsed since the last full calibration.
6.5 Heat Source:
6.5.1 Electric Heater - A hot plate or immersion heater provided with a variable transformer or other device suitable for regulating the temperature of the heating element.
6.5.2 Gas Heater - A bunsen-type burner, fitted with a chimney.
7. Sampling
7.1 Samples from shipments shall be taken in accordance with Practice D140 and shall be free of foreign substances. Thoroughly mix the sample before removing a representative portion for the determination or for dehydration.
7.2 If the presence of water is indicated by surface foam on heating, maintain the sample at a temperature of about 260 °F (125 °C) in an open container until the surface is free of foam. Take care not to overheat, and remove from the heat source as soon as the foam has subsided.
8. Test Specimens
8.1 Coat the inner surfaces and core pins of the mold very lightly with silicone oil or silicone grease. Form the pitch into truly shaped cubes either by pressing (8.2) or by pouring (8.4), the latter being preceded by melting (8.3) if the sample is solid. Use an excess of pitch in either case. Cool until firm and remove the surplus material by drawing the heated blade of a putty knife or spatula across the surface of the mold so that the cubes are pressed into the cavities. Then open the mold and remove the cubes carefully to avoid distortion. Inspect each specimen for possible cracks or bubbles and reject any which are not perfect.
8.2 Pitches with softening points up to about 140 °F (60 °C) can usually be pressed into the mold by hand at, or slightly above, room temperature. If too soft, they may be pressed under water at about 40 °F (5 °C).
8.3 To melt a dry pitch sample, add the material to a container having a height equal to or exceeding its width and a volume of not less than 50 mL, until it is about half full. Place the container on a hot plate, or in an oven or bath. Do not use an open flame for melting pitch. After melting is complete, stir gently but thoroughly, avoiding the incorporation of air bubbles. The maximum temperature should not exceed the expected softening point by more than 90 °F (50 °C). Any foam that forms shall be skimmed off.
8.4 Pour a slight excess of the liquid pitch into the mold with the lip of the container close to the surface so as to minimize the entrainment of air bubbles. Underpouring past the blade of a spatula is helpful in this respect. Even small bubbles markedly affect the weight of the cube and the observed softening point. Cool the specimens in the mold until firm, under cold water if necessary; then trim and inspect the cubes as directed in 8.1.