10. Procedure
10.1 Proceed to 10.2.1 if optional blending is explicitly required by the lubricant specification (see Note 9).
NOTE 11 - Lubricant specifications that require optional blending use the term "Option A" to identify this process.
10.2 Vigorously hand shake the container for 1 min before decanting approximately 200 mL of sample into a 400-mL beaker. Mix the sample with the lab mixer (see 6.5) for 60 s +/- 10 s at 500 +/- 100 rpm. If optional blending is not required, proceed to 10.3.
10.2.1 Optional Blending - Clean the container of the 1 L (1 qt), high-speed blender (see 6.9). Vigorously hand shake the sample container for 1 min. Place 500 mL of sample into the container, cover, and blend at maximum speed for 1 min. Because it is normal for considerable air to be entrained during this agitation, allow to stand in a temperature controlled environment of 24 +/- 3°C until entrained bubbles have dispersed and the temperature of the oil has reached 24 +/- 3°C. Within 3 h following the agitation, continue testing at 10.3.
10.2.2 In case of viscous oils, 3 h can be insufficient time to eliminate the entrained air. If a longer time is required, record the time as a note on the results.
10.3 Heat the sample for 30 min in a convection oven set at 49 +/- 3°C.
10.4 Allow the sample to cool to room temperature (23 +/- 4°C). The test shall be performed within 3 h of the heating step.
10.5 Fill the 1000 mL graduated cylinder to the 180 mL level.
10.6 Lower the cylinder into the bath to at least the 900 mL mark in a bath capable of maintaining the sample at 150 +/- 1°C. Proceed with 10.9 within 1 h of this step. Exercise care in lowering the cylinder into the hot oil. Lower the cylinder slowly to avoid cracking of the bottom of the cylinder.
10.7 Temporarily immerse a thermometer or other temperature sensor into the oil sample to determine correct sample temperature. Allow sufficient time for the sample to warm up to 150 +/- 1°C.
10.8 With the air inlet disconnected, immerse the gas diffuser into the sample. Adjust the position of the diffuser, touching the center of the bottom of the cylinder. Allow the diffuser to soak for at least 5 min and proceed only when the sample temperature reaches 150°C +/- 1°C.
10.9 After the 5 min soak, record the level of the initial top volume (V1), if required, to the nearest 10 mL, connect the air inlet to the gas diffuser and adjust the entering flow rate to 200 +/- 5 mL/min. Force compressed air through the gas diffuser at this rate for 5 min +/- 10 s.
10.10 Just before disconnecting the air source, record the final total volume (V2), the static foam volume, and the kinetic foam volume to the nearest 10 mL as shown in Fig. 1.
10.11 After disconnecting the air supply, record the static foam volume in mL, as shown in Fig. 1, at any of the time(s) selected from the following list of options.
Option 1: 5 s (+/-1.0 s)
Option 2: 15 s (+/-1.0 s)
Option 3: 1 min (+/-1.0 s)
Option 4: 5 min (+/-1.0 s)
Option 5: 10 min (+/-1.0 s)
10.12 Record the seconds (+/-1 s) required for the foam to collapse to "0" after the 5 min blowing period.
11. Calculations and Results
11.1 Total Volume Increase:

11.2 Percent Total Volume Increase:
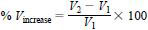