8. Sample Preparation
8.1 Use the crushing procedure in 8.2 and subsequent paragraphs so that contributions to VBD from both as-calcined and laboratory-crushed particles (which differ significantly in density) are included. Do not remove dedust oil from the sample prior to sample preparation or testing.
NOTE 2 - Because the vibrated bulk density method is based on the packing of sized particles, the method of sample preparation can affect results due to differences in particle shapes affecting packing characteristics.
8.1.1 Air-dry the laboratory sample, if it appears to be wet, prior to crushing to avoid caking.
NOTE 3 - On agreement by purchaser and supplier, density of only as-calcined particles in the selected size range are determined. If so, proceed to Section 11 and report as part of the result that only as-calcined particles were used.
NOTE 4 - Recommended practice for collecting samples and the equipment and procedures for dividing are described in Test Methods D346, D2013, D2234/D2234M, and D4057 and Practices D6969 and D6970.
8.2 Jaw Crusher Operation - Use the procedure appropriate to the jaw crusher being used, adjust the jaws so that the gap between them (at their closest position to each other in the crushing cycle) is approximately 5 mm. Turn on the jaw crusher motor, slowly feed the sample through the jaw crusher, and collect the product for further reduction through a roll crusher. In this step, the entire gross sample shall pass through the jaw crusher.
8.3 Roll Crusher Operation - (Warning - To avoid damage to the rolls, size reduction with the roll crusher must be limited to a maximum ratio of 4 to 1. Depending on the fraction desired, a one-step reduction is often not possible from the maximum particle size in the jaw crusher product and intermediate roll settings are used. The sample is reduced to the desired mesh size using as few intermediate settings as possible (but not exceeding the 4 to 1 reduction ratio).
8.3.1 With the motor deactivated, and using a method appropriate to the roll crusher being used, adjust the roll gap according to the following procedure. If the rolls are readily accessible, adjustment with a leaf-type feeler gage inserted between the rolls with the motor deactivated is useful.
8.3.2 Calculate the ratio of the maximum particle size of the roll crusher feed (expressed as the opening, in millimetres, of the finest screen through which the largest particles will pass) to the maximum particle size of the bulk density fraction required (expressed as the opening, in millimetres, of the coarser of the two screens used to define the bulk density fraction).
8.3.3 Select the number of crushing steps required from the following table:
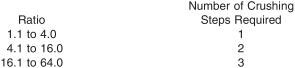
8.3.4 For each crushing step required, the roll gap is decreased (from a value equivalent to the maximum particle size of the feed) by a factor of:
n√Ratio (as defined in 8.3.2)
where:
n = number of crushing steps required (8.3.3)
8.3.5 For example, it is desired to reduce a coke having a maximum particle size of 6.68 mm to one having a maximum particle size of 0.208 mm. The calculation is as follows:
Ratio = 32.115 (see 8.3.2)
Crushing steps required = 3 (see 8.3.3)
Factor = 3√32.115 = 3.179 (see 8.3.4)
1st setting: 6.68 mm / 3.179 = 2.101 mm
2nd setting: 2.101 mm / 3.179 = 0.661 mm
3rd setting: 0.661 mm / 3.179 = 0.208 mm
8.3.6 After the roll gap is adjusted, remove the feeler gage (if used), turn on the roll crusher motor, slowly feed 0.3 kg of the jaw crusher product through the roll crusher, and collect the sample. When more than one roll crushing step is required, regrind through smaller openings the entire 0.3 kg sample, and collect the sample. Do not sieve the sample between crushing steps. Then, using the appropriate screens (those defining the bulk density fraction), sample receiver, and cover, sieve the roll-crushed sample in the sieve shaker for 15 min, as required by Test Method D5709, Table 3. With this final roll crusher setting, at least 30 % of the coke generally will be in the desired particle size range. A sieve shaker shall be used for the final sieving step to remove the undersize. Do not use other means of removing the undersize. Do not overload the screen as described in Test Method D5709, subsection 9.5. Overloading a screen occurs when too much material is on a screen and prevents a particle from touching the screen and having the opportunity to pass through the screen. For a 200 mm diameter screen and calcined petroleum coke, the quantity is approximately 200 g.
8.3.7 This setting will produce roughly equal weights of coke coarser and finer than the desired fraction, provided that the starting material is sufficiently coarse. If yield is at least 30 % and the ratio of coarser to finer product is between 0.8 and 2.0, crushing is satisfactory and the remainder of the material is fed through the roll crusher, using as many intermediate settings as required. The entire roll crusher product is consolidated and the desired fraction separated.
8.3.8 At the roll gap setting intended to maximize the final product, proceed as follows if the criteria in 8.3.7 are not met. If after one pass the ratio of coarser to finer-than-desired coke is greater than 2.0, decrease the roll gap to 80 % of its original value and test another 0.3 kg sample of jaw crusher product or intermediate roll crusher product, if required. (If the product is just slightly too coarse, an alternative procedure is to make multiple passes through the roll crusher with the original gap setting.)
8.3.9 If the ratio is less than 0.8 and the starting material is coarse enough to permit this ratio to be attained, increase the roll gap by 20 % of its original value and retest with 0.3 kg of jaw crusher product or intermediate roll crusher product, if required. If the starting material is not coarse enough to obtain this ratio for the particle size range selected for the test, disregard this restriction.
8.3.10 These procedures will result in a satisfactory sample as defined in 8.3.7 in the majority of cases. If not, adjust roll settings or make multiple passes, or both, with trial-and-error adjustments until a satisfactory composite sample is obtained from the 2-kg starting sample. Observe that 0.3-kg fractions of the jaw crusher product can be discarded in their entirety if too fine after roll crushing. Partial consolidation of roll crusher products is not acceptable; that is, once a 0.3-kg sample of jaw crusher product has been passed through the roll crusher, it must either be consolidated in its entirety with other roll crusher products or discarded. A minimum of 210 g of properly sized vibrated bulk density sample is required.
9. Preparation of Apparatus
9.1 Graduated Cylinder - Since vibrator amplitude is affected by weight on the table, cut off the graduate below the pouring lip so that the weight is 215 +/- 10 g. Sand sharp edges. With one common brand of graduated cylinder, this corresponds to an overall length of about 305 mm. Fit the graduate with a No. 8 stopper (tight fit).
9.2 Vibrator - Fasten the cork ring securely with screws to the table top of the vibrator as a retainer ring for the graduated cylinder during the test. (Drill and tap holes in the vibrator table as required.) The inner diameter of the cork ring is intentionally larger than the base width of the graduated cylinder. It is designed only to keep the graduated cylinder from vibrating off the vibrator table. Do not attach the graduated cylinder to the vibrator by a clamp or other device. The graduated cylinder shall vibrate freely.
10. Calibration of Apparatus
10.1 Graduated Cylinder Calibration Factor - Measure the distance, in millimetres, between the 90-mLand 170-mLmarks on the graduated cylinder.
B = 170 - 90/distance in mm
where:
B = calibration factor, mL/mm.
Wrap a piece of masking tape around the graduate with the 190-mL mark at the bottom of the tape. Make eight marks on the bottom of the tape equidistantly around the cylinder. These are used only for equally spacing height measurements (not as a volume measurement base line).
10.2 Determination of Accuracy of Graduated Cylinder - Using distilled water at 25 +/- 5°C, fill the graduate to the 90-mL mark and determine the weight of water at that volume. Using a density of 0.997 g/cm3 for water, determine the true volume. Do the same at 20-mL increments up to the 170-mL mark. If the deviation at any indicated volume is greater than +/- 0.5 mL, a table of indicated volumes versus true volumes should be made for use in computing bulk density.
10.3 Vibrator - Using a hex wrench, remove the four screws that hold the vibrator table and remove the table. Loosen the core locking screw. If the aluminum table is grounded, remove the ground wire. Turn the vibrator on its side and attach the ohmmeter to the table support and ground. Turn the core into the case (clockwise) until the ohmmeter registers zero (core is touching armature). Back off the core (counter-clockwise) until the ohmmeter reads infinite resistance. Mark the zero position with arrows on each side of the screw slot and turn the core out exactly one and three-eighths turns. Replace the table and tighten the four screws.