5. Procedure A - Additive Effects on Fuel
5.1 Base Fuel required for Procedures A and B must meet the Jet A or Jet A-1 requirements of Specification D1655 and be clay treated in accordance with the procedure of Test Method D3948, Appendix X1, "Preparation of Reference Fluid Base". It should exhibit a rating of 98 WSIM after clay treating by Test Methods D3602 or D3948. About 75 L (20 gal) of base fuel is required for Procedures A and B. Store the base fuel in clean epoxy-coated metal containers and recheck the WSIM rating after 3-months' storage.
5.2 Prepare the test fuel by blending four times the maximum recommended concentration of the additive into 38 L (10 gal) of base fuel.
NOTE 2 - If the maximum solubility level is below this concentration, prepare the test fuel accordingly.
5.3 All ASTM D1655 specification tests and the following additional tests, should be run on the base fuel and the test fuel:
D3602 or D3948 water separation
D2624 electrical conductivity
D156 Saybolt color bright and clear-visual inspection
5.4 If tests on test fuel exceed the limits of D1655, rerun a second test fuel containing only the maximum recommended concentration of additive in accordance with 5.3 and report.
6. Procedure B - Additive Compatibility with Other Additives 6.1 Prepare duplicate test blends by mixing 100 mL of base fuel containing four times the maximum recommended concentration of the candidate additive to 100 mL of base fuel containing, in turn, each of the previously approved additives (other than oxidation inhibitors) at four times their maximum recommended concentrations. The resultant blend contains two times the maximum recommended concentration of each additive.
NOTE 3 - Approved additives are listed in Specification D1655 but Procedure B may also be applied to additives approved for aviation fuels by other organizations.
6.2 Divide each of the mixtures described in 6.1 into two clear, tall glass containers (100 mL each). Put the duplicate samples into dark, cold storage at -17.8°C (0°F) for 24 h. Inspect immediately after removal from cold storage, for indications of precipitation, cloudiness, darkening, or other visual evidence of incompatibility.
6.3 Warm the samples inspected from cold storage, shake to remix any separated components, and hold at 38°C (100°F) for 24 h. Inspect them again for visual evidence of incompatibility immediately after cooling to room temperature. Keep fuel samples in dark storage during conditioning and between inspections.
NOTE 4 - Photographs are a useful record of results of compatibility testing.
7. Procedure C - Additive Compatibility with Fuel System Components
7.1 Formulate the jet reference liquid required for conducting fluid immersion tests as follows:
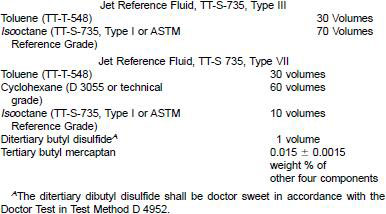
7.1.1 When tested for mercaptan and total sulfur in accordance with Test Methods D3227 and D1266, respectively, the reference fluid shall have the following properties:
Mercaptan sulfur content, 0.0050 +/- 0.0005 weight %
Total sulfur content, 0.400 +/- 0.005 weight %
Store the fluid out of contact with light in containers that are inert to the fluid ingredients. (Welded aluminum, nongalvanized welded steel, or glass containers are suitable.) If not used within 90 days after blending, retest the fluid for mercaptan and total sulfur content.
7.2 Prepare reference test fluids by blending four times the maximum recommended concentration of the additive into the specified Jet Reference Fluid.
7.3 Fuel system materials subject to immersion tests in Jet Reference Fluid and in Reference Test Fluid are listed in Table 1.
7.4 Detailed testing procedures for each class of fuel system components appear in Research Report D02-1137 on file in ASTM Headquarters. When conducted by an approved laboratory, these testing procedures provide data acceptable to aircraft manufacturers or other approving agencies.
7.5 In general, each fuel system material is subject to special application and curing techniques and then each test specimen is immersed in both the specified Jet Reference Fluid and Reference Test Fluid containing additive for varying times at specified temperatures. These details as well as the techniques for inspecting specimens for failure are described in Research Report D02-1137.