7. Procedure
7.1 Melt the asphalt sample and pour into the preheated brass softening point ring, allow to cool, and trim off the excess asphalt from each face of the ring as described in Test Method D36.
7.1.1 It is important that the lower face and rim of the ring (16-mm (40/64-in.) inside diameter) be clean and that the asphalt disc completely fill the ring and be flush with the lower face. There should be no trace of any release agent which may have been used on the pouring plate (see Test Method D36) on either the lower face of the ring or the asphalt.
7.2 Place the filter paper on the flat support plate and put the filled and trimmed softening point rings on the paper with the 16-mm (40/64-in.) diameter asphalt disc face in contact with the paper. Each ring should be no closer than 40 mm (1.5 in.) from the edge of the filter paper or from another ring.
7.2.1 The known material (Note 3) must be placed on the same piece of filter paper and support plate as the sample(s) being tested.
NOTE 3 - The "known" material for the purpose of this test is a material whose staining tendency is known to the investigator and which is used to compare with the material being tested (see also Note 6).
7.2.2 Identify each asphalt sample and known material by appropriately marking the filter paper in pencil near each ring.
7.3 Place the entire assembly on the support plate in the oven, preheated to 80 ± 1°C (175 ± 2°F), and allow to remain at that temperature for 120 ± 1 h.
7.4 Remove the assembly on the support plate from the oven and allow to cool to room temperature (about 24°C (75°F)).
7.5 Remove the ring and the asphalt disc from the filter paper taking care to avoid tearing of the paper.
7.6 Determine and record the average of three measurements, taken at about 120° apart, of the diameter of the stained circle on the filter paper expressed numerically in 0.4-mm units (64ths of an inch) to the nearest 0.4 mm (1/64 in.) using a steel rule.
7.6.1 Alternatively, use the hole template and determine the diameter of the hole which best fits the stained circle on the filter paper and record the result numerically in 0.4-mm units (64ths of an inch) to the nearest 0.4 mm (1/64 in.).
8. Calculation and Interpretation of Results
8.1 Subtract the initial diameter of the asphalt disc expressed numerically in 0.4-mm units (64ths of an inch), that is, 40 from the average, or best fit, diameter of the stained circle on the filter paper expressed numerically in 0.4-mm units (64ths of an inch) to obtain the stain index.
NOTE 4 - If the dimensional measurements have been made in metric units, the average diameter must be converted to inch units at this point in order to compute the numerical value for stain index which is derived from the diameter expressed numerically in 64ths of an inch.
NOTE 5 - Example: If the average, or best fit, diameter of the stained circle on the filter paper is 19.5 mm (49/64 in.), then the stain index = 49 - 40 = 9.
8.2 Interpretation of Results - The following ranges of stain index have been determined to represent the staining tendency of asphalts used in the production of asphalt roofing shingles.
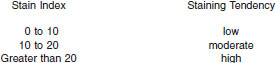
The staining tendency in roofing products is strongly influenced by storage conditions especially temperature and time, by the pressure generated in stacked material from the mass of material in the overlying stack, and by the nature, amount, and distribution of backsurfacing material.