ASTM D2670 standard test method for measuring wear properties of fluid lubricants (Falex pin and Vee block method)
8. Calibration of Load Gages
8.1 Apparatus with 800-lb or 3000-lb Gage:
8.1.1 Remove the Allen set screw and 1/2 in. (12.70-mm) ball from the left jaw socket (Fig. 4).
8.1.2 Insert the special Allen screw with the attached 10-mm Brinell ball into the working face of the left jaw. Adjust so that ball projects about 5/32 (approximately 4 mm) from face of jaw.
8.1.3 Insert the back-up plug in the counterbore of the right-hand jaw. Adjust so that the plug projects about 1/32 in. (approximately 0.8 mm) from the face.
8.1.4 Support the standard test coupon so that the upper edge of the coupon is about 3/32 in. (approximately 2.5 mm) below the upper surface of the jaws. Place a steel rule across the face of the jaws. Adjust the Allen screw with the attached 10-mm ball until the face of the jaws are parallel to the steel rule with the test coupon in position for indentation.
8.1.5 With the test coupon in position for the first impression, place the load gage assembly on the lever arms.
8.1.6 Place the loading arm on the ratchet wheel and actuate the motor. Allow the motor to run until the load gage indicates a load of 200 lb. A slight takeup on the ratchet wheel is required to hold the load due to the ball sinking into the test coupon. After a 200-lb load is obtained, hold for 1 min for the indentation to form.
8.1.7 Turn off the machine and back off the load until the test coupon is free from the jaws. Advance the test coupon approximately 3/8 in. (approximately 9.5 mm) (additional indentations should be separated by a minimum distance of 2.5 x the diameter of the initial indentation). Check the alignment of the jaws, and repeat the procedure described in 8.1.6 at gage loads of 400, 600, and 800 lb when using an 800-lb gage. If a 3000-lb gage is used, check at 800, 1500, and 2500 lb.
8.1.8 Remove the load gage assembly and test coupon and measure the diameter of each indentation to 0.01 mm with a microscope. Make three measurements of the indentation diameter, rotating the test coupon to ensure that no two measurements represent the same points. Average the three measurements of each impression and record.
8.1.9 Plot the four impression readings versus gage load readings on log-log paper (K and E 467080 or equivalent). From the plot determine the gage load reading corresponding to an impression diameter of 3.30 mm. Typically, this gage load reading will be about 700 lb. This gage load shall be used in Section 12. A typical plot of impression diameter versus gage readings is shown in Fig. 5.
8.2 Apparatus with 4500-lb Gage - Use the same procedure as with 800-lb gage, above, except obtain impressions at gage readings of 300, 500, 750, and 1000 lb. Plot the impression readings and determine the gage load corresponding to an impression diameter of 3.30 mm. Typically, this gage load reading will be about 900 lb. This gage load shall be used in the procedure, (Section 13). Fig. 4 includes a typical plot of impression diameter versus gage readings for the 4500-lb gage.
9. Test Standards Check
9.1 Prepare a blend containing 0.10 weight % of sulfur, precipitated powder, USP, and 99.90 weight percent white mineral oil,6 USP, having a viscosity at 100°F (37.8°C) of 340 to 390 SUS (73.4 to 84.2 cSt). Heat the blend, in a glass beaker, to 240 to 250°F (116 to 121°C) and stir (glass stirrer) for 15 min. Designate this mixture as Blend A.
9.2 Prepare, similarly, a blend containing 0.20 weight % of sulfur and 99.80 weight % of white mineral oil. Designate this mixture as Blend B.
9.3 Refer to Section 8 for recommended use of these standards.
10. Apparatus and Testing Check
10.1 The purpose of this check is to establish that the apparatus is in satisfactory condition and that the test is being run in conformance to the procedure covered in Section 13. For such check purposes the fluid standards covered in Section 9 should be used (Note 3). The average of triplicate runs on the fluid standards should fall within the following limits (Note 4):
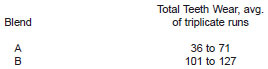
Repeatability of test data should conform to precision limits set forth in Section 15.
NOTE 3 - Three commercial cutting oils were initially chosen as reference fluid standards. These were replaced by the specified white oil-sulfur blends because of greater availability, uniformity, and purity. Results of the cooperative tests on the cutting oils are covered in Appendix X1.
NOTE 4 - These limits were derived from data in Appendix X1. The limits shown for Blend A are the minimum and maximum averages obtained in the Series 2 tests. Essentially the same averages were obtained in the Series 1 and 3 tests.
The limits shown for Blend B are the minimum and maximum averages obtained in the Series 1 tests. Essentially the same averages were obtained in the Series 3 tests.
11. Test Conditions
11.1 The test shall be conducted under the following conditions (Note 5):

NOTE 5 - Although the test can be run under other test conditions, the precision limits described in Section 14 apply only to tests conducted under the conditions shown above and the procedure specified in Section 13.
12. Preparation of Apparatus
12.1 Thoroughly clean the V-blocks, test journals, lubricant cup, and supports for V-blocks and test journals by washing with the solvent selected in 7.2.5. Dry the V-blocks, test journals, lubricant cup, and supports, by allowing the solvent to evaporate in air.
12.2 After cleaning, handle the test pieces with care to prevent contamination. Particularly, avoid contact of fingers with mating surfaces of V-blocks and test journals.