ASTM D2596 for standard test method for measurement of extreme-pressure properties of lubricating grease (Four-Ball method)
1. Scope
1.1 This test method covers the determination of the load-carrying properties of lubricating greases. Two determinations are made:
1.1.1 Load-Wear Index (formerly called Mean-Hertz Load), and
1.1.2 Weld Point, by means of the Four-Ball Extreme-Pressure (EP) Tester.
1.2 The values stated in SI units are to be regarded as the standard. The values in parentheses are for information only.
1.3 This standard does not purport to address all of the safety concerns, if any, associated with its use. It is the responsibility of the user of this standard to establish appropriate safety and health practices and determine the applicability of regulatory limitations prior to use. Specific precautionary statements are given in 7.1 and 7.2.
2. Referenced Documents
2.1 ASTM Standards:
D235 Specification for Mineral Spirits (Petroleum Spirits) (Hydrocarbon Dry Cleaning Solvent)
2.2 American National Standard:
B3.12 Metal Balls
3. Terminology
3.1 Definitions:
3.1.1 compensation line, n-a line of plot on log-log paper where the coordinates are scar diameter in millimetres and applied load in kilograms-force (or Newtons) obtained under dynamic conditions.
3.1.1.1 Discussion—Shown in Fig. 1 as line ABE.
3.1.2 compensation scar diameter - the average diameter, in millimetres, of the wear scar on the stationary balls caused by the rotating ball under an applied load in the presence of a lubricant, but without causing either seizure or welding.
3.1.3 corrected load, n-the load in kilograms-force (or Newtons) obtained by multiplying the applied load by the ratio of the Hertz scar diameter to the measured scar diameter at that load.
3.1.3.1 Discussion - In this test method, the corrected load is calculated for each run.
3.1.4 hertz line, n-a line of plot on log-log paper where the coordinates are scar diameter in millimetres and applied load in kilograms-force (or Newtons) obtained under static conditions.
3.1.4.1 Discussion - Shown in Fig. 1 as a hertz line.
3.1.5 hertz scar diameter, n-the average diameter, in millimetres, of an indentation caused by the deformation of the balls under static load (prior to test). It may be calculated from the equation:
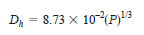
where:
D(h) is the Hertz diameter of the contact area in millimetres and P is the static applied load in kilograms-force.
3.1.6 immediate seizure region, n-that region of the scar-load curve characterized by seizure or welding at the startup or by large wear scars.
3.1.6.1 Discussion - Under conditions of this test method, the immediate seizure region is shown by line CD. Also, initial deflection of indicating pen on the optional friction-measuring device is larger than with nonseizure loads.
3.1.7 incipient seizure or initial seizure region, n-that region at which, with an applied load, there is a momentary breakdown of the lubricating film.
3.1.7.1 Discussion - This breakdown is noted by a sudden increase in the measured scar diameter, shown in Fig. 1 as line BC, and a momentary deflection of the indicating pen of the optional friction-measuring device.
3.1.8 last nonseizure load, n-the last load at which the measured scar diameter is not more than 5 % greater than the compenation value at that load.
3.1.8.1 Discussion - Shown in Fig. 1 as Point B.
3.1.9 load-wear index (or the load-carrying property of a lubricant), n-an index of the ability of a lubricant to prevent wear at applied loads.
3.1.9.1 Discussion - Under the conditions of this test, specific loadings in kilograms-force (or Newtons) having intervals of approximately 0.1 logarithmic units, are applied to the three stationary balls for ten runs prior to welding. The load wear index is the average of the corrected loads determined for the ten applied loads immediately preceding the weld point.
3.1.10 weld point, n-the lowest applied load at which sliding surfaces seize and then weld.
3.1.10.1 Discussion - Under the conditions of this test, the lowest applied load in kilograms-force (or Newtons) at which the rotating ball seizes and then welds to the three stationary balls, indicating the extreme-pressure level of the lubricating grease has been exceeded. See Fig. 1, Point D.
3.1.10.2 Discussion - Some lubricating greases do not allow true welding, and extreme scoring of the three stationary balls results. In such cases, the applied load which produces a maximum scar diameter of 4 mm is reported as the weld point.